Бутылочное горлышко (bottleneck, или «узкое место») – участок в производственной цепочке, на котором возникает перегрузка. Предыдущий и последующий узлы могут работать эффективнее, но данный конкретный элемент уже загружен на 100%.
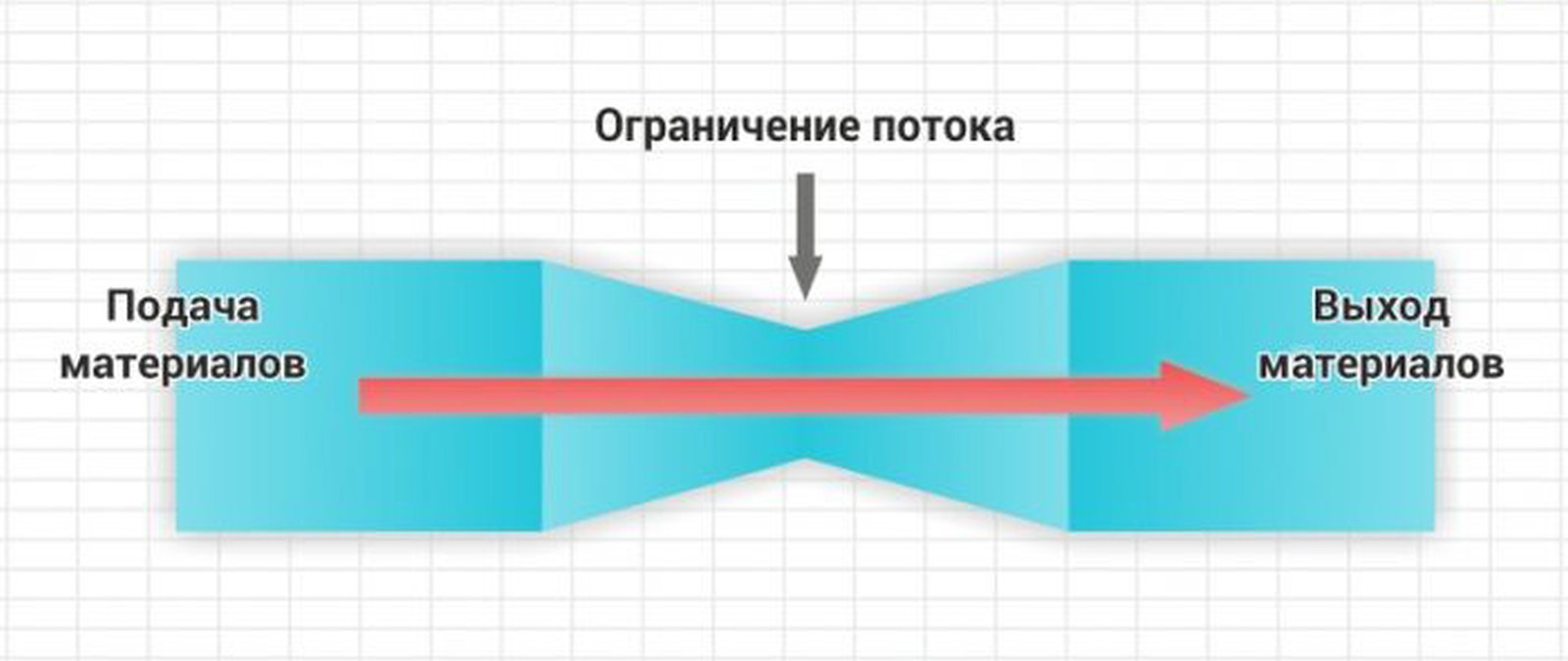
«Бутылочные горлышки» могут быть разными – внешними и внутренними, временными (уход в отпуск ключевого сотрудника) и постоянными, связанными со сбытом, логистикой, складом и т.д. Но наиболее частая причина ограниченных возможностей производства – полная загруженность дорогих станков или иного сложного оборудования.
Если станок используется 100% рабочего времени и не справляется с заказами, то тут уж, кажется, ничего не поделаешь – только покупать еще один. Но это только на первый взгляд.
О недостатках «простых» решений
Самый очевидный и действенный вариант устранить узкое место в производственной цепочке – купить новое дополнительное оборудование. Простое и эффективное решение… если есть кому за него заплатить. Ведь каждый станок стоит несколько сотен тысяч, а то и миллионов рублей.
Кроме того, иногда предприятие в целом справляется с объемами заказов, а задача увеличить выпуск продукции возникает только в короткий период пикового спроса. Эта ситуация полна неразрешимых противоречий. Новое оборудование будет работать только пару месяцев в году – а значит, и срок окупаемости вложенных средств окажется неприемлемо долгим. Но если не удовлетворить вовремя запросы клиентов, то часть из них перейдет к конкурентам, причем не на пару месяцев, а навсегда.
И не будем забывать про санкции – покупка западного оборудования сейчас происходит по схемам параллельного импорта, а это дополнительное удорожание и сложности с внедрением.
Нарастить производительность и повысить эффективность оборудования без капитальных вложений на имеющемся парке станков – вот настоящий вызов для отечественных предприятий!
Обнаружение бутылочных горлышек — нетривиальная задача
Если станок работает без остановок, а перед ним скопилась груда заготовок, то очевидно, что именно здесь и есть критически узкое место производства.
Но на больших заводах, где сотни агрегатов работают в сложной взаимосвязи друг с другом, обнаружить перегруженные участки бывает очень непросто. Возникает «накопительный эффект» – сразу несколько точек на производственной линии выпускают чуть больше заготовок, чем способно переработать оборудование на следующем шаге.
Это приводит к тому, что проблема становится «плавающей». Сегодня перегружен «Станок А», завтра – «Станок Б», а на третий день все работает гладко и без задержек. На первый взгляд серьезных проблем нет, а выпуск продукции при этом ниже расчетного.
Бывают и совсем неожиданные причины. Например, многолетняя статистика четко подтверждает – производительность ночных смен на 5-15% ниже, чем дневных. Такая картина наблюдается на самых разных предприятиях и даже в разных странах. В отсутствие начальства снижается уровень дисциплины. И вроде бы все работают, а результат хуже, чем ожидалось.
Строго говоря, дисциплинарные проблемы не относятся к «бутылочным горлышкам», но, по большому счету, какая разница, по каким причинам завод не работает на полную мощность. Итог-то все равно один – недополученная прибыль, сорванные сроки и растущая себестоимость продукции.
Выход из трудной ситуации – повышение эффективности оборудования путем внедрения объективной системы контроля производства. Такой, как Энкост Мониторинг, который обнаружит скрытые резервы предприятия и даст возможность нарастить выпуск готовой продукции на 15-30% без капитальных вложений.
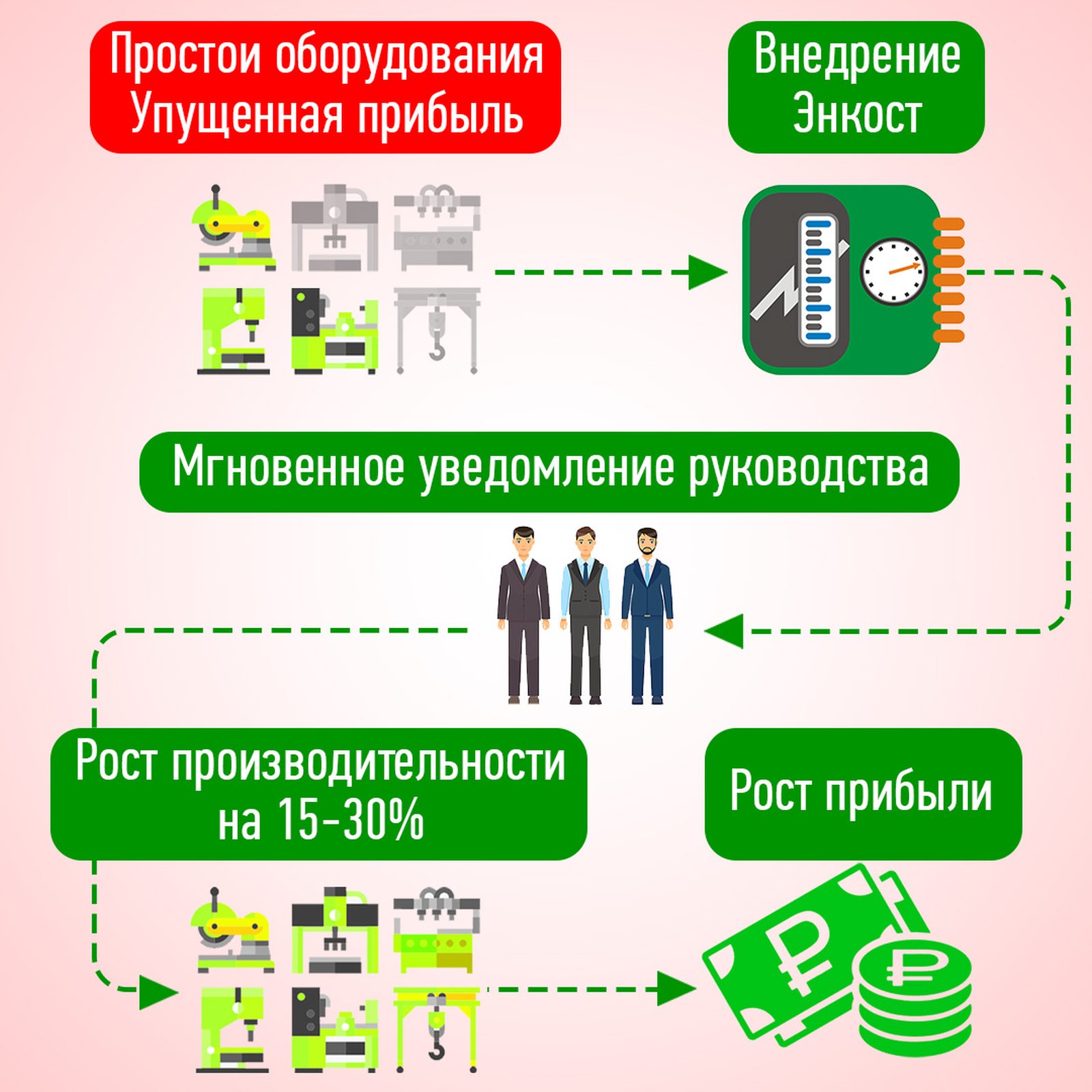
В основе работы Энкост Мониторинг лежит инструмент, который называется «токоизмерительные клещи».
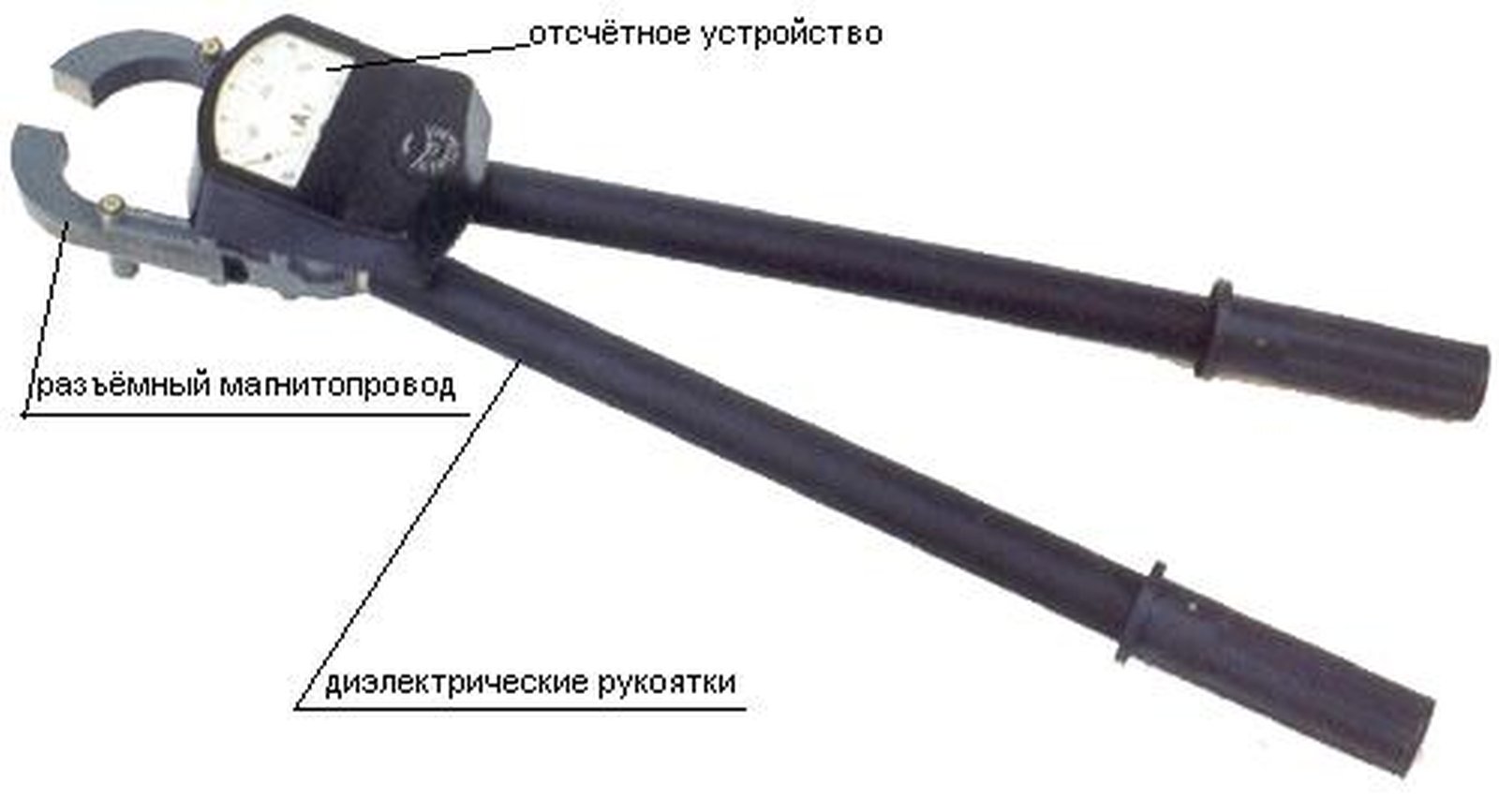
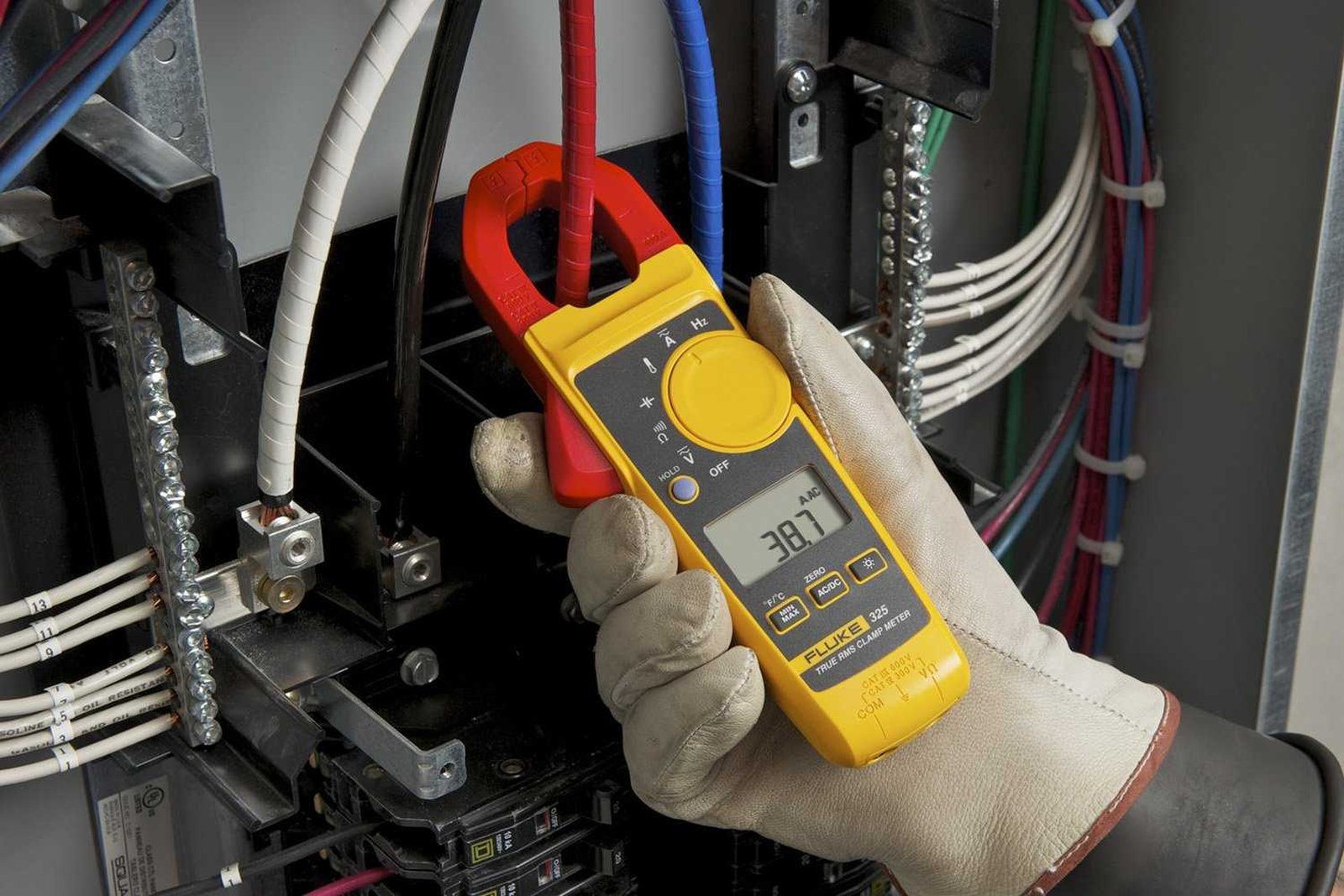
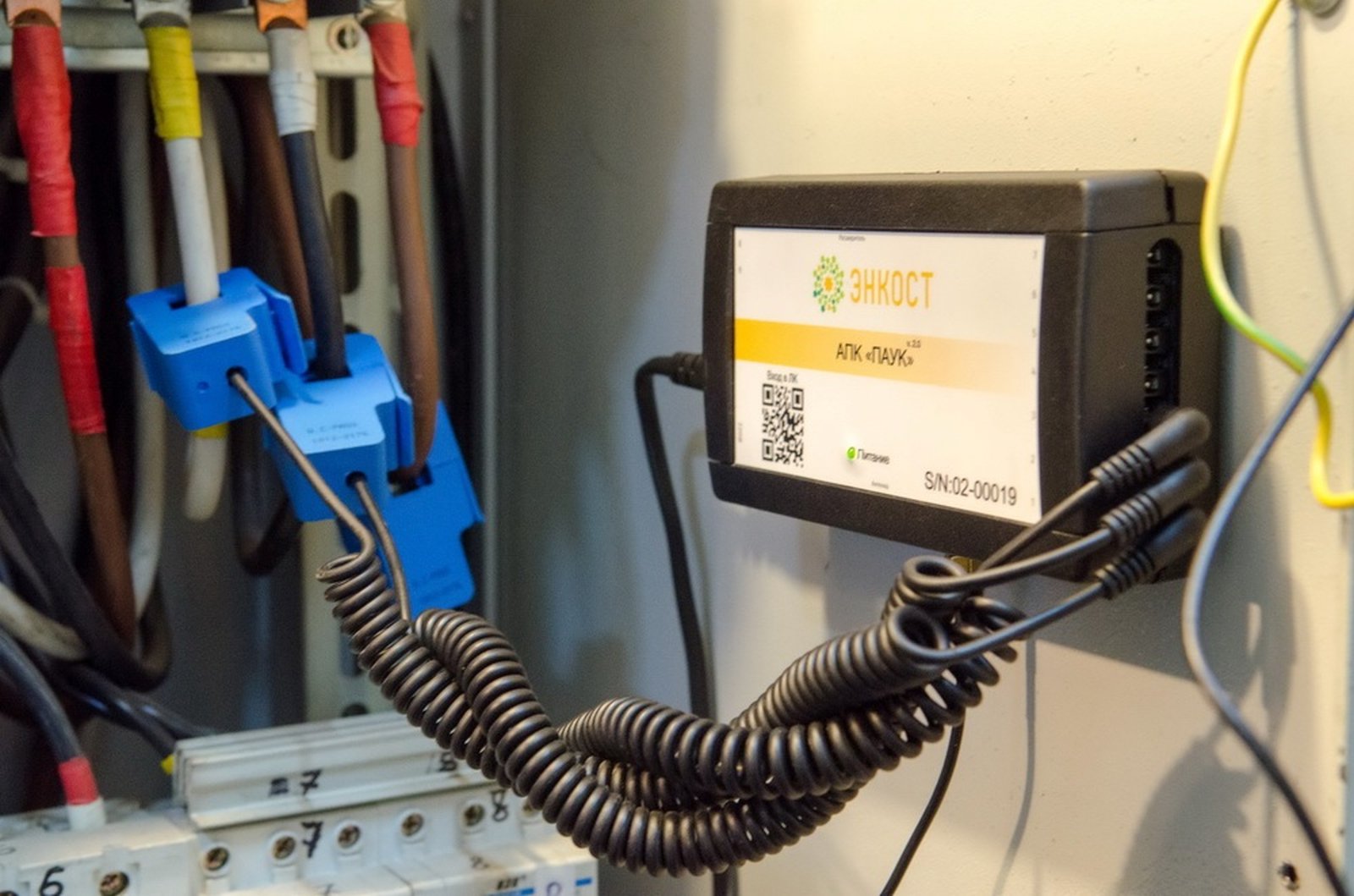
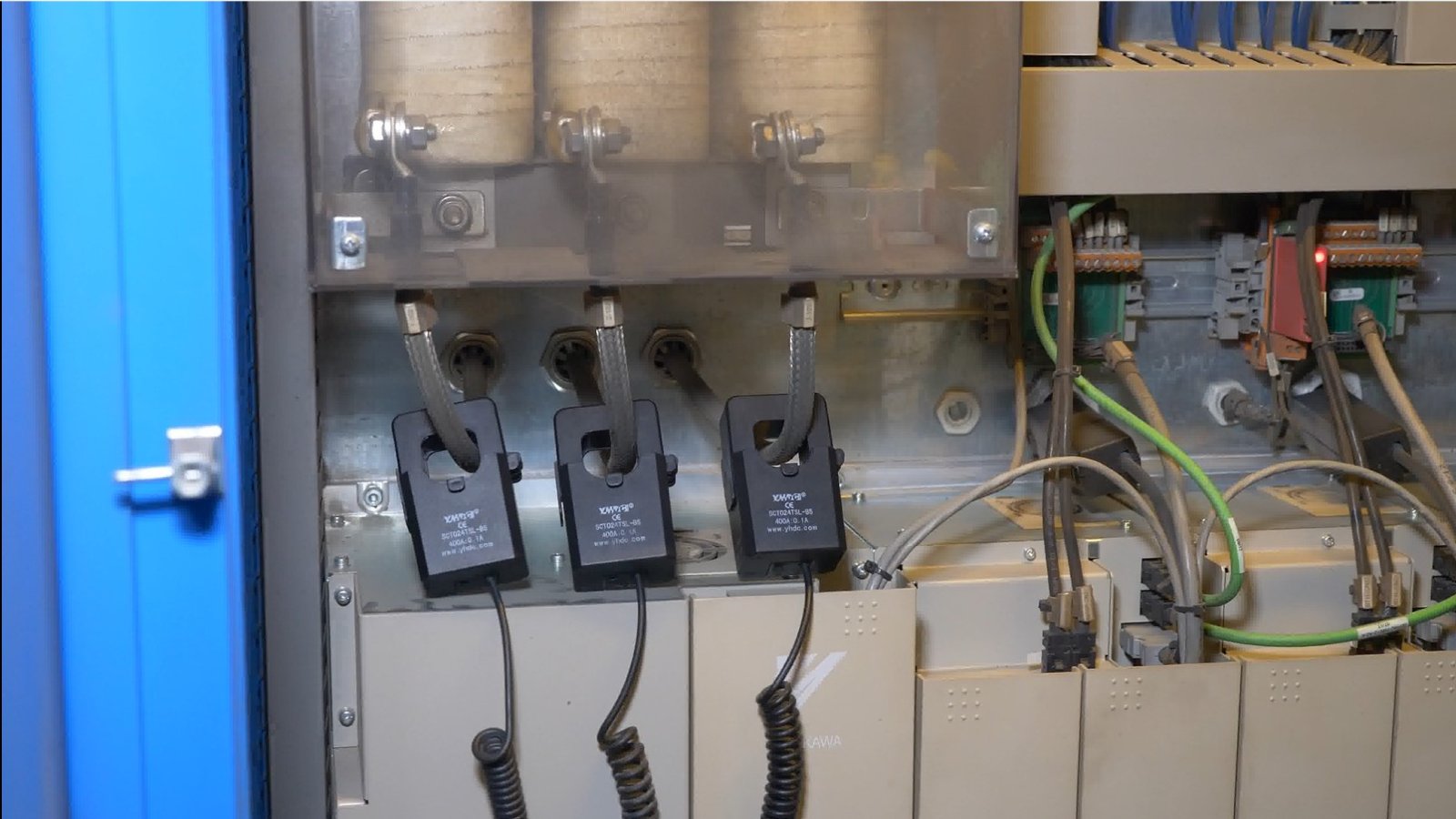
Токовые клещи закрепляются поверх силового кабеля и замеряют силу тока – это дает возможность определить текущее состояние станка (работа – холостой ход – остановка). Данные измерений передаются на сервер (аппаратный модуль «Паук»), который собирает статистику и формирует отчеты в режиме реального времени.
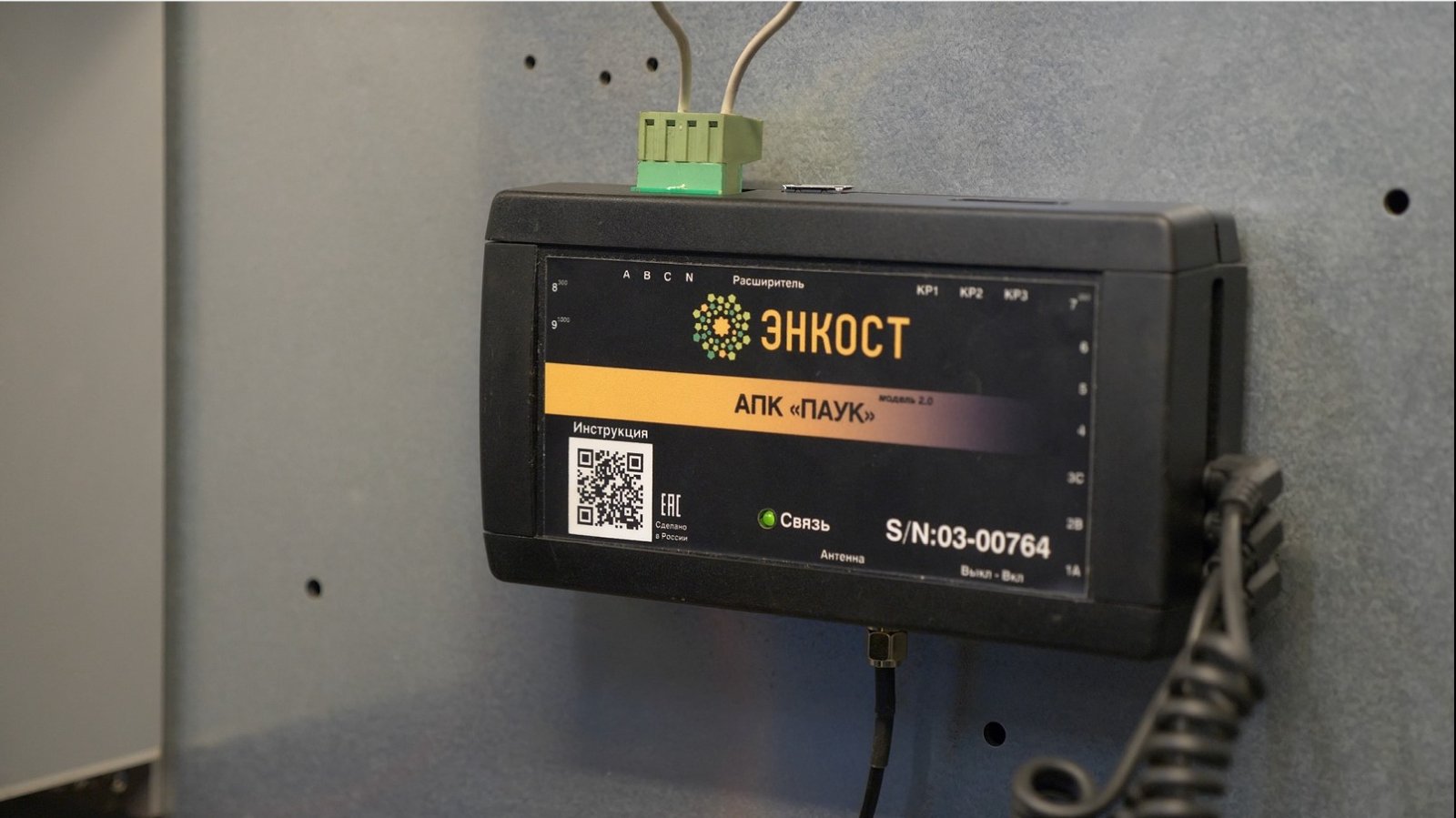
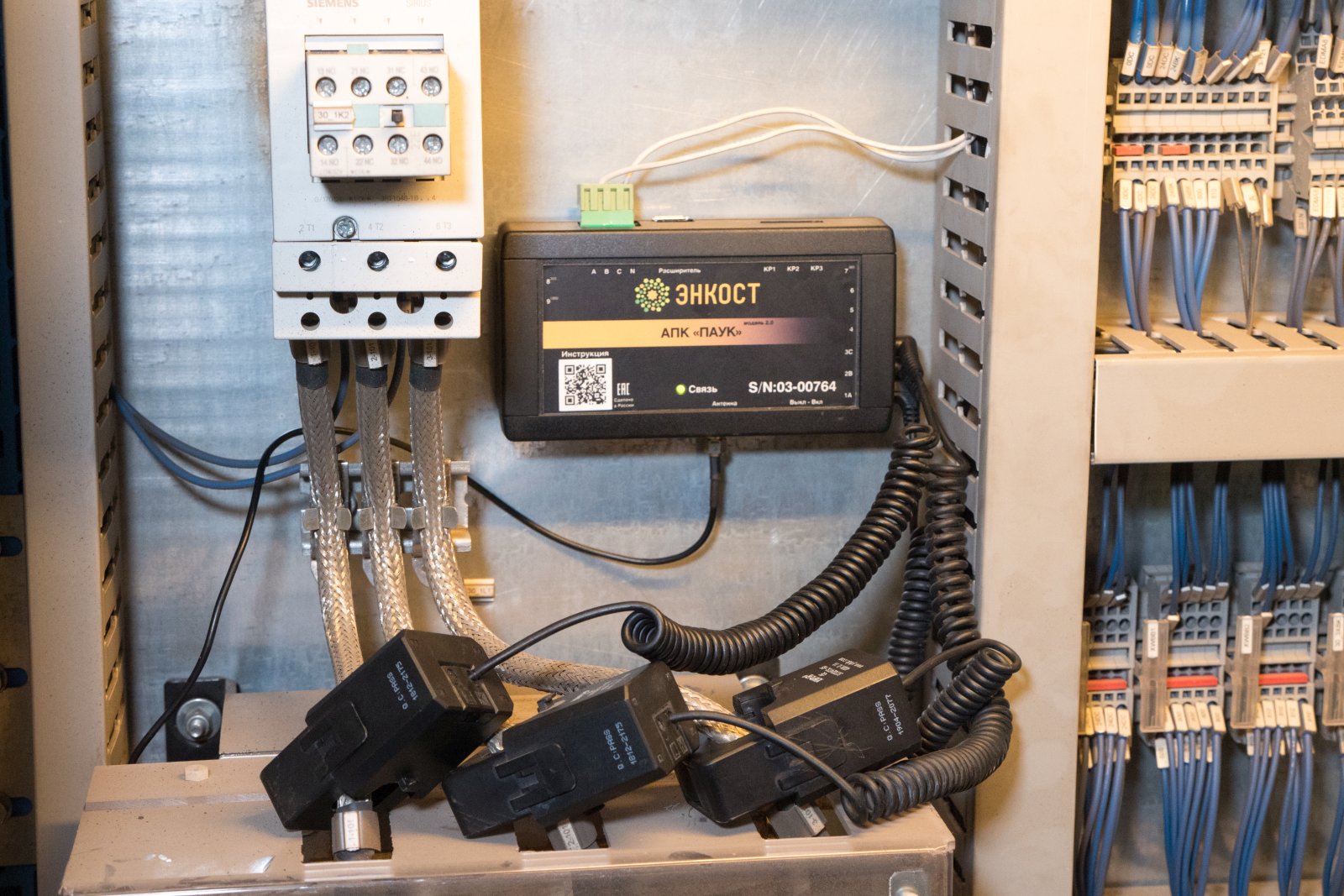
Привычные всем бумажные отчеты о закрытии смены составляют в конце рабочего дня и часто делают это методом «от обратного». Например, вместо 400 единиц продукции за смену выпустили только 340, т.е. на 15% меньше запланированного. Значит, в статистику запишем соответствующий простой станка и придумаем для этого какую-то уважительную причину. Автоматические отчеты Энкост Мониторинг полностью исключают искажения, связанные с человеческим фактором.
На каждый станок крепится смартфон с настроенным телеграм-ботом. При остановке оборудования оператор станка сообщает конкретную причину простоя – выбирает один из стандартных вариантов (нет сырья, остановка на ремонт, завершение смены) либо дает иное пояснение.
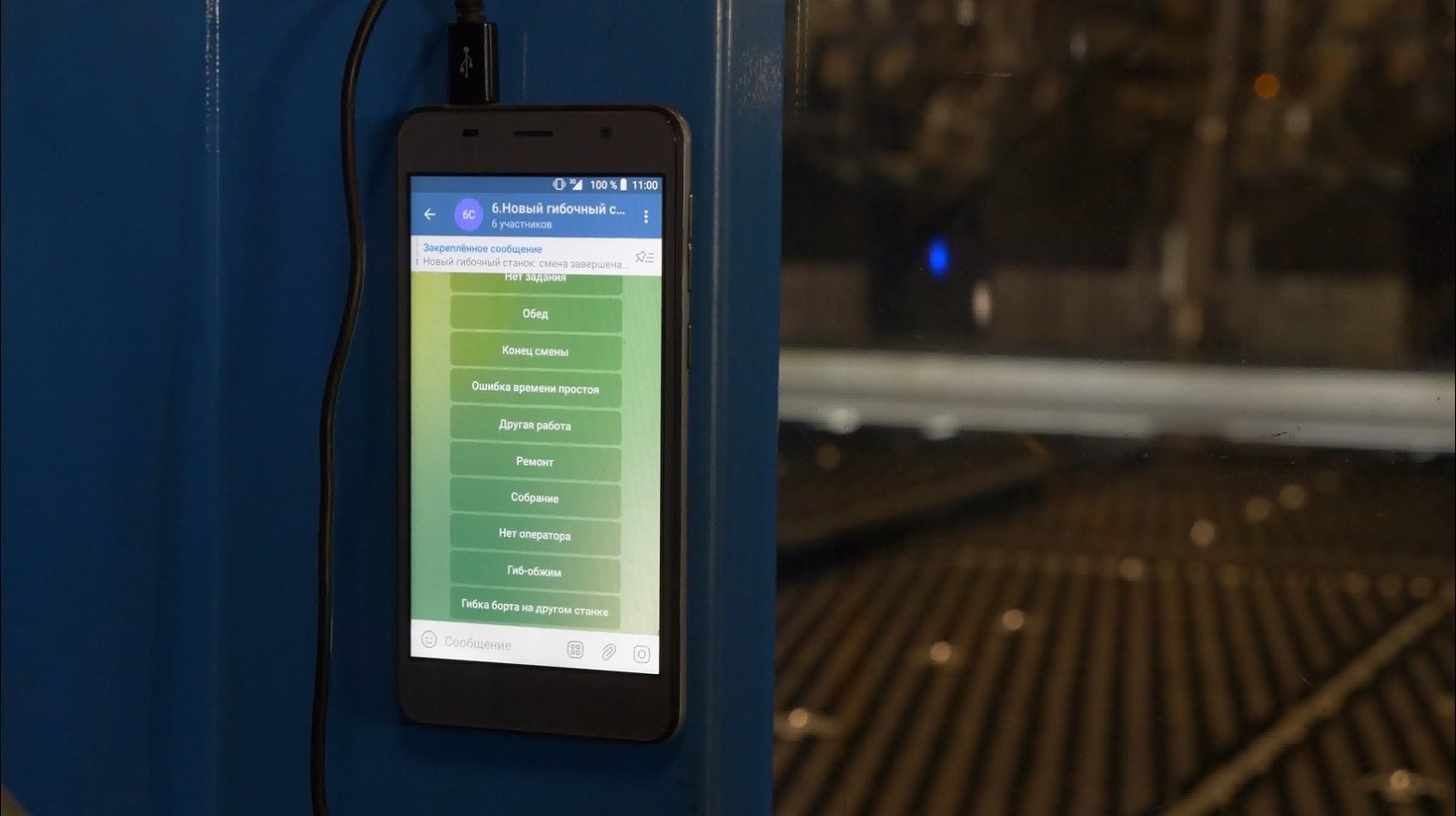
На совсем короткие (менее 3-5 минут) остановки указывать причину необязательно (такой режим можно активировать в настройках), но в общую статистику они все равно попадут.
Помимо контроля состояния оборудования путем измерения силы тока, можно интегрировать в систему мониторинга различные дополнительные датчики – оптические (ведут визуальный подсчет продукции), тензорные (измеряют массу) и другие. Дополнительное измерительное оборудование подбирается с учетом особенностей конкретного производства.
Важнейшее преимущество системы Энкост Мониторинг — внедрение без остановки предприятия. Токоизмерительные клещи снимают данные о силе тока без разрыва электрической цепи. Дополнительные датчики и сервер «Паук» также являются внешним оборудованием, разбирать и даже временно останавливать станки для запуска Энкост не потребуется.
Механизм эскалации уведомлений
Быстрое вовлечение руководства в процесс решения проблем – простой, но очень важный элемент системы мониторинга, который показал удивительную эффективность.
Если оборудование остановилось, то мгновенные уведомления уходят начальнику смены и в профильные службы (снабженческую при нехватке сырья, сервисную в случае поломки и т.д.). Если за разумное время проблема не решена внутри цеха, то уведомления идут дальше по цепочке – сначала начальнику производства, затем главному инженеру и т. д. вплоть до собственника предприятия.
Двойной эффект эскалации уведомлений:
- руководители быстро включаются в процесс решения проблемы, о которой иначе узнали бы только на следующие сутки из итоговых отчетов;
- работники текущей смены стараются решить проблему максимально быстро, пока уведомления не ушли начальству.
Причины простоев, которые быстро выявит Энкост Мониторинг
Отсутствие сырья или заготовок. Простои по этой причине означают либо плохую работу склада и снабженцев либо «затор» на одном из предыдущих участков производственной цепочки. Отчеты дадут ясный ответ на вопрос, где искать корень проблемы.
Излишняя бюрократия, недостаточная оптимизация процессов производства. Например, станок простаивает по причине отсутствия оператора, который в это время находится на очередном совещании. Или (еще лучше!) занят условной уборкой снега, на которую отправили текущую смену.
Примеры немного утрированные (хотя и абсолютно реальные), но, вообще, нерациональное использование рабочего времени сотрудников – одна из главных причин низкой производительности.
Неудовлетворительное качество сервисного обслуживания. Рассмотрим два «говорящих» примера из данных о работе сервисных служб.
Пример 1: ремонт занял всего лишь 7 минут, но время ожидания до прихода сотрудников сервисного отдела составило 40 минут. Налицо незначительная проблема, с которой оператор станка не смог справиться самостоятельно. Но нерасторопность сервисников привела к длительной остановке оборудования.
Пример 2: сервисные инженеры прибыли к остановившемуся станку за 4 минуты (отличный результат). Ремонт занял 1 час (норма). Но вот ожидание начала ремонта составило 3 суток! Явная причина такой длительной задержки – отсутствие на складе запасных частей. А это повод задать следующий вопрос: данную запчасть действительно невозможно было заказать заранее, или же мы имеем недоработку сервисников (не подали вовремя заявку) или снабженцев (не закупили).
Низкий уровень дисциплины. Перекуры, опоздания и внеплановые перерывы могут легко занять до 25% рабочего времени.
Обычно с этим пытаются бороться внедрением системы видеонаблюдения, электронных пропусков, штрафов и т.д. Но все эти методы работают откровенно неважно. То же видеонаблюдение подходит только для анализа спорных ситуаций постфактум, но для постоянного контроля процессов производства неприменимо, ведь всего 10 камер — это уже 240 часов видео каждый день, для просмотра которого необходим дополнительный персонал.
И только бездушные датчики Энкост обеспечивают 100% уровень контроля и дисциплины. Каждый сотрудник «привязан» в отчетах к своему станку и не имеет возможности просто так покинуть рабочее место. Даже попытка оставить станок включенным не поможет устроить лишний «перекур» – система тут же зафиксирует длительный период холостого хода.
Отчеты и статистика
Все данные доступны удаленно через личный кабинет в любое время суток. Можно делать выборки и срезы по предприятию в целом, конкретному цеху, производственной линии или станку. После внедрения Энкост Мониторинг собственник всегда будет в курсе того, что происходит на его предприятии.
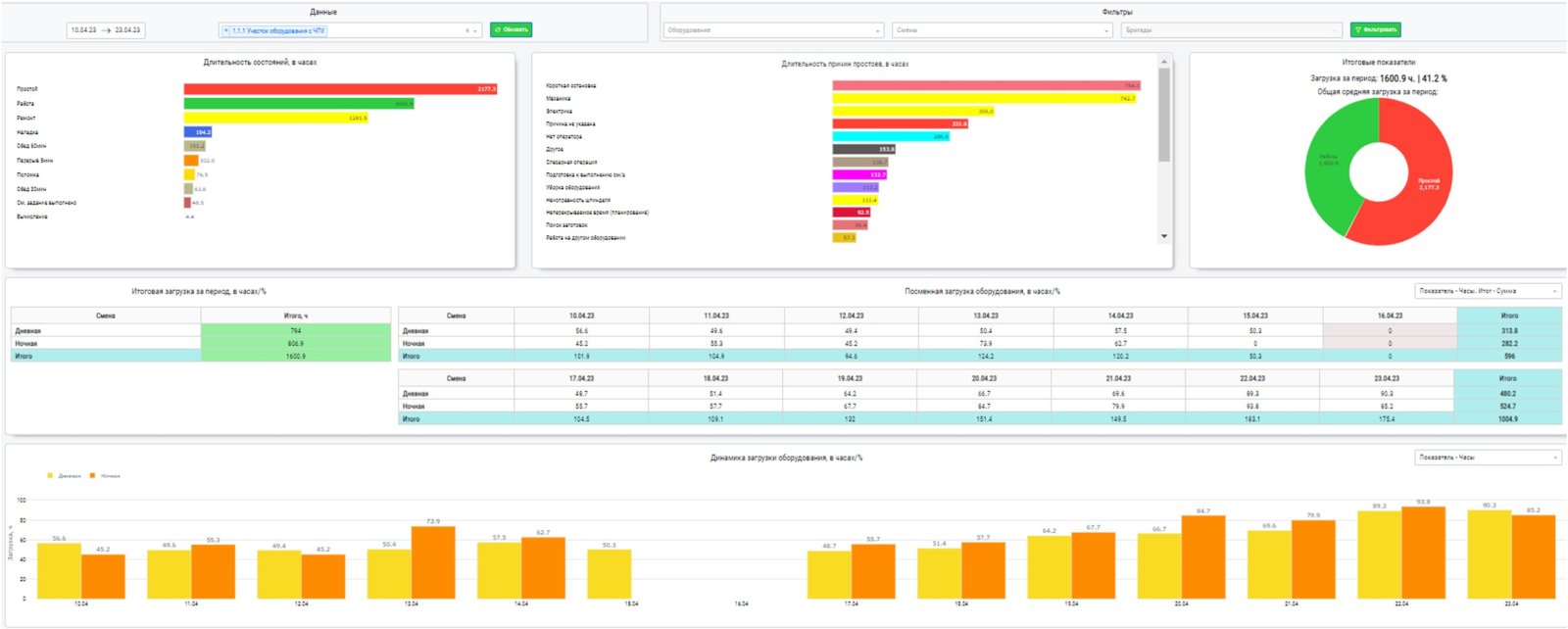
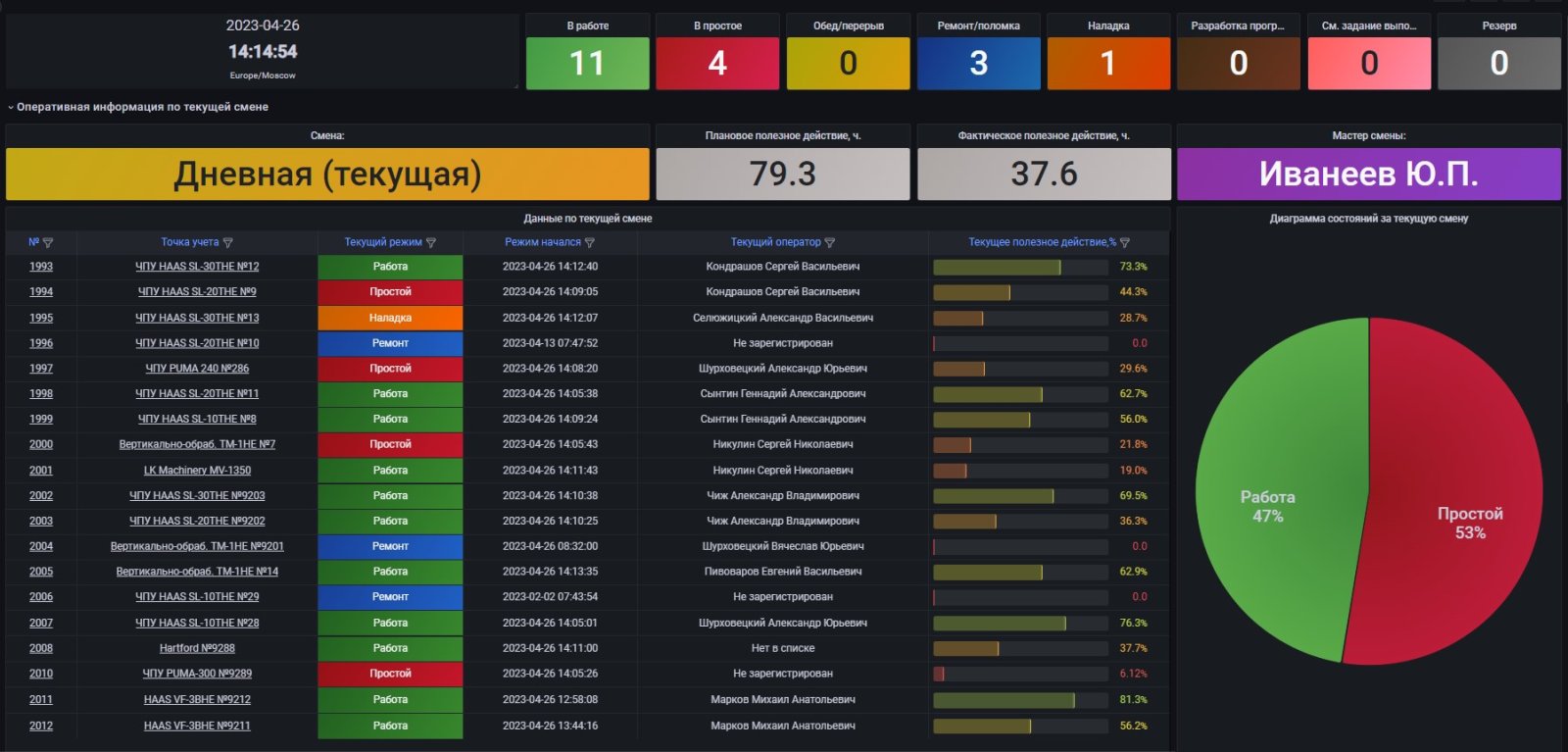
Также отчеты можно выгружать в более привычный некоторым пользователям формат Excel.
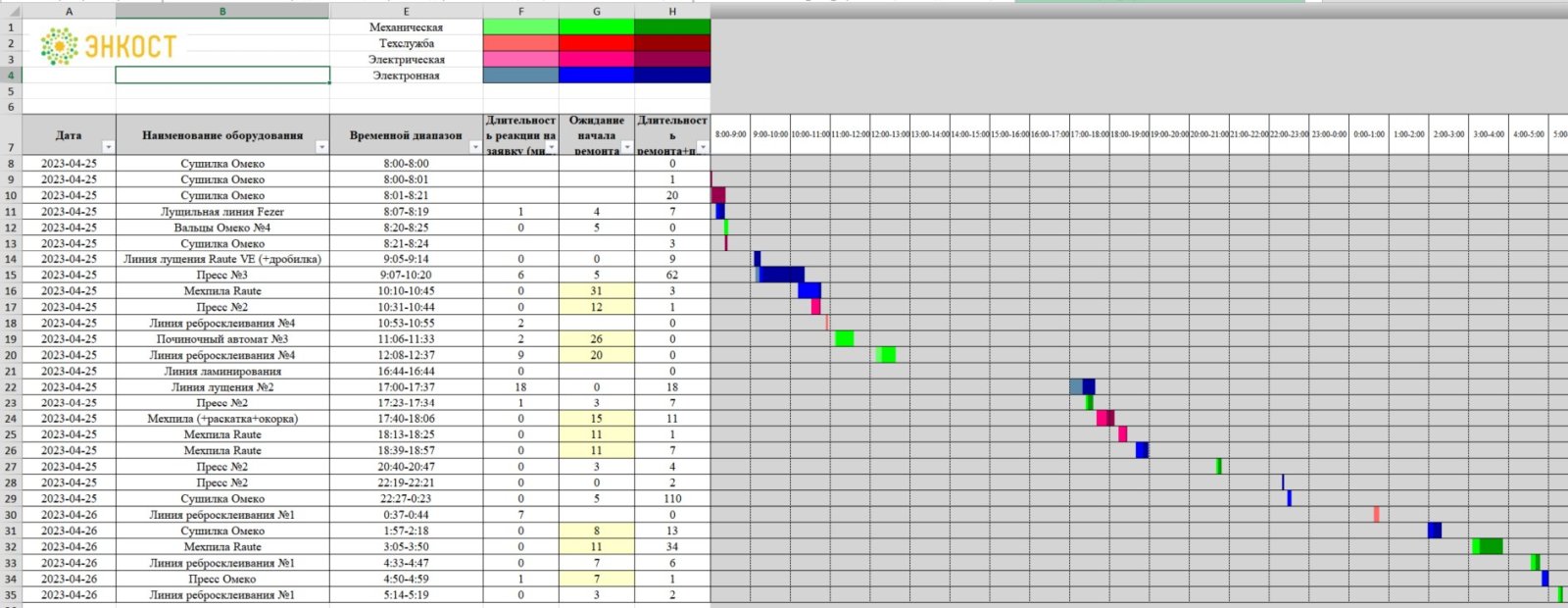
Отдельная группа отчетов дает четкую картину работы сервисной службы предприятия.
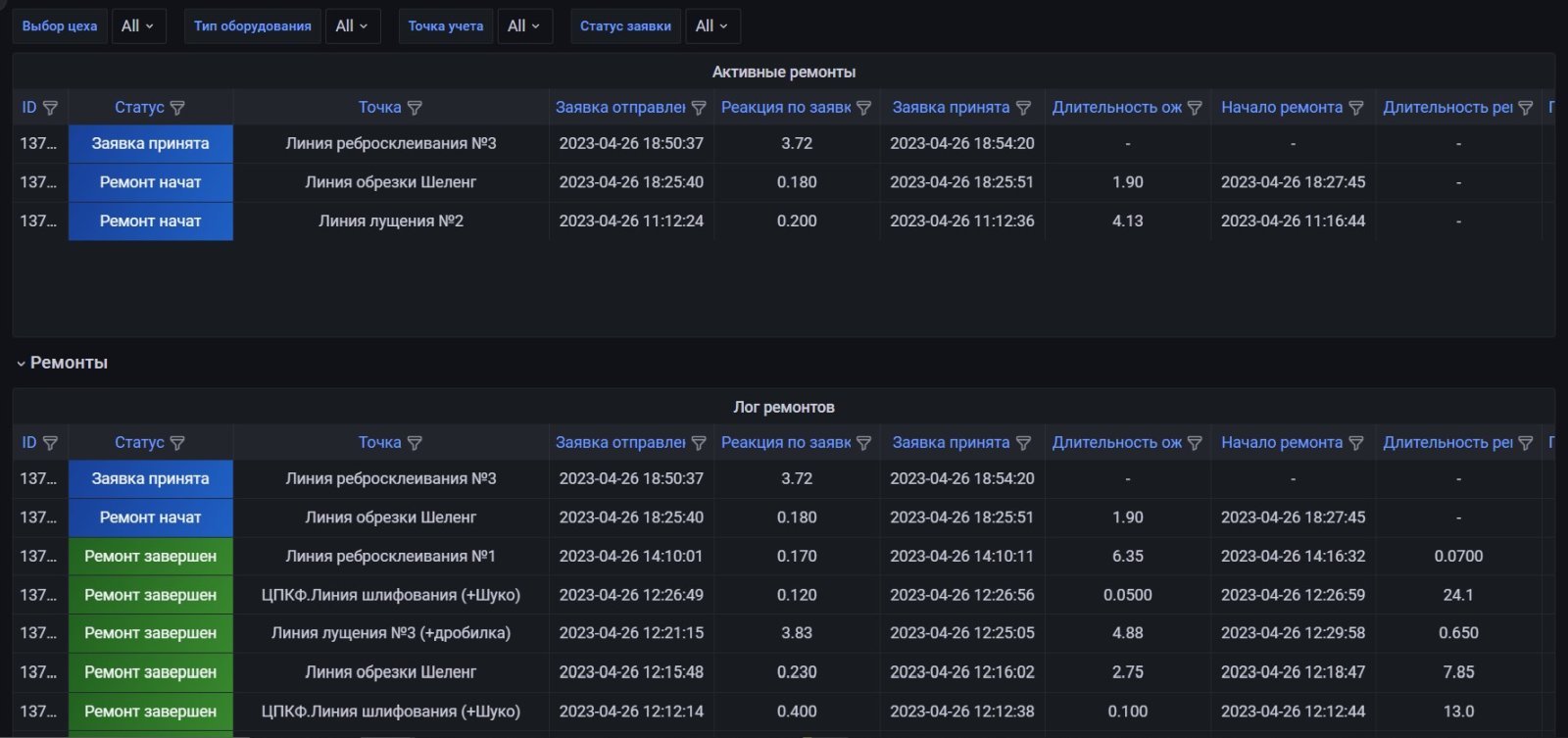
Выгоды от внедрения Энкост Мониторинг
1. Разовая экономия миллионов рублей на покупке нового оборудования. Внедрение объективного мониторинга легко «выжмет» еще 15-20% производительности из существующего (якобы полностью загруженного) оборудования. В результате получится избежать приобретения новых дорогих станков.
Эта экономия – разовая, но зато сразу на огромную сумму, поэтому мы вынесли ее первым пунктом.
Но, строго говоря, основная миссия Энкост Мониторинг – не экономить, а больше зарабатывать. Об этом все остальные пункты данного раздела.
2. Оптимизация производства и снижение простоев без капитальных вложений. Две стороны одной медали – если на 15-20% уменьшились простои, то и выпуск готовой продукции увеличился на ту же величину.
Распорядиться этой дополнительной эффективностью можно по-разному:
- увеличить прибыль (больше произвели – больше продали – больше заработали);
- снизить цену на товар за счет уменьшения себестоимости и захватить большую долю рынка;
- предложить лучшие среди конкурентов сроки выполнения заказа.
3. Улучшение работы технических и сервисных служб. Дополнительный контроль, о котором мы рассказывали выше, а также правильное распределение заявок (не по времени поступления, а по важности для предприятия) уменьшают время нахождения станков в ремонте.
4. Повышение дисциплины и выработки, особенно во время ночных смен. Здесь все просто. Любой рабочий твердо знает, что утром на руках у директора будет полный и объективный расклад по работе смены. По каждому отдельному станку и каждому конкретному оператору. А потому никуда не денешься – приходится работать в полную силу.
5. Быстрое обнаружение даже сложных комбинированных «бутылочных горлышек». Эту ситуацию мы описывали в самом начале статьи. Каждый конкретный станок вроде бы недогружен большую часть времени и только изредка не справляется с потоком заготовок. Явных проблем не заметно, а линия в итоге выпускает на 20-30% меньше продукции, чем планировалось.
С помощью изучения статистических данных, полученных от системы Энкост Мониторинг, получится быстро обнаружить истинные причины недостаточной производительности.
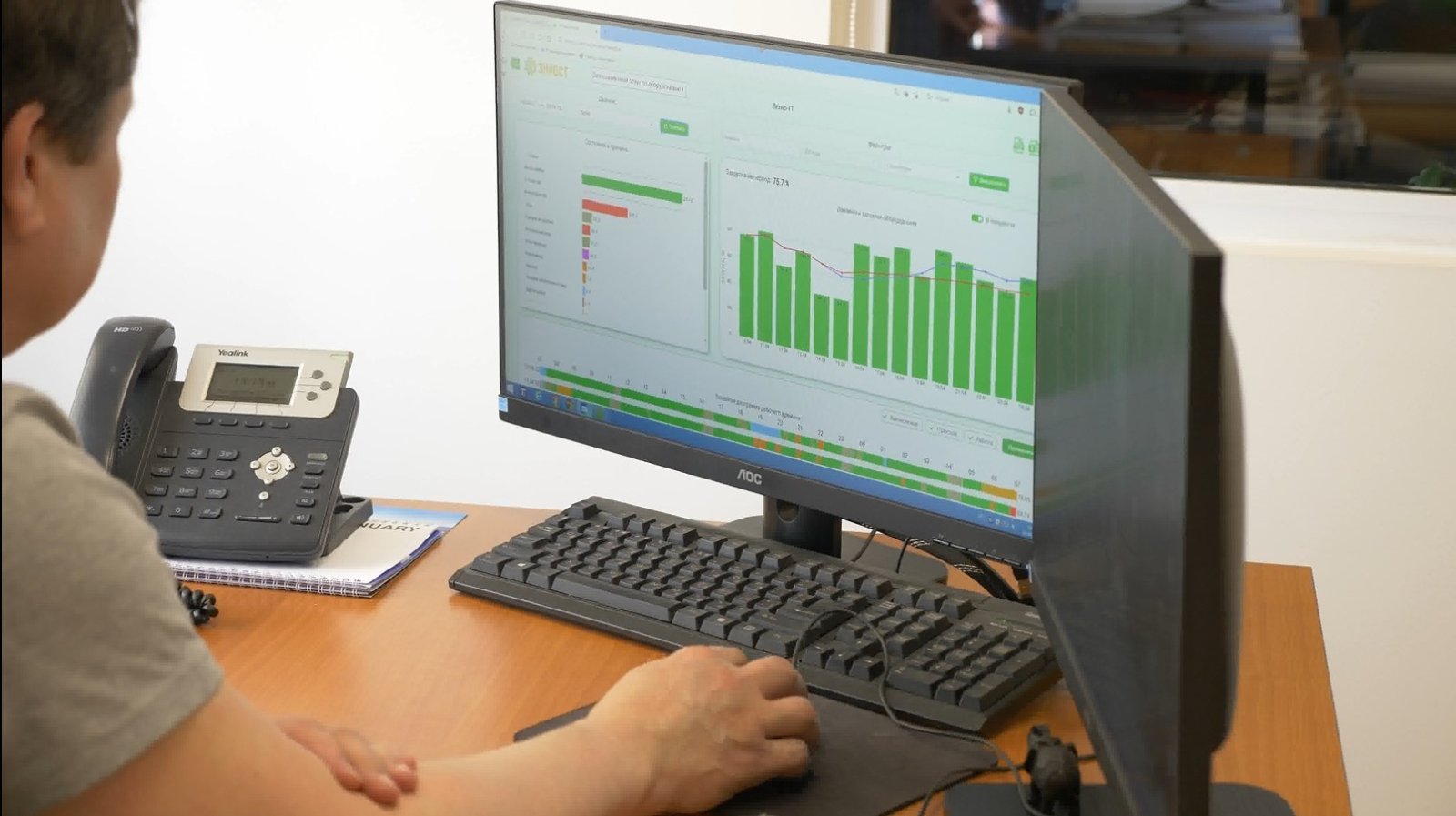
6. Оперативное подключение руководства к решению проблем – работает описанный выше механизм эскалации уведомлений.
7. Тестирование гипотез, оптимизация управления производством. Установка Энкост Мониторинг в конкретных цифрах показывает сравнительную картину до/после применения новых стратегий развития предприятия. И если эти цифры окажутся удручающими, то детальный анализ отчетов покажет причину неудачи.
В 100 раз дешевле конкурентов?!
Да, на старте система мониторинга станков Энкост дешевле аналогов на два порядка. Потому что это сервис на основе месячной подписки. Такая модель определяет ряд критических преимуществ перед конкурентами.
1. Минимальные стартовые расходы (~50 тыс. руб. однократно). Стоимость мониторингового оборудования составляет 300-500 тыс. руб. на один только станок. Т.е. даже небольшому предприятию с парком из 10 единиц техники потребуется 3-5 миллионов рублей, чтобы внедрить полноценную систему мониторинга. В случае с Энкост все оборудование предоставляется в бесплатную аренду в рамках стандартного тарифного плана (от 35 тыс. руб./мес.).
На начальном этапе потребуется компенсировать только командировочные расходы сотрудников компании – около 50 тысяч рублей однократно. За первые две недели использования системы (тестовый период) оплата не взимается.
2. Нет скрытых и непредвиденных трат. Покупкой мониторинговой техники расходы не ограничиваются. Любая система требует доработок под нужды конкретного предприятия. А это дополнительное оборудование и десятки часов работы программистов, которые тоже придется оплачивать. В Энкост Мониторинг все эти работы включены в стоимость действующего месячного тарифа.
3. Риск неудачного внедрения — 0%. Более всего пользу от установки систем мониторинга понимают технические специалисты среднего звена – инженеры и IT-специалисты. Но они не участвуют в принятии решений.
Идти же с новым предложением к руководству рискованно, ведь при отсутствии внятного результата обвинять в пустых многомиллионных тратах будут инициатора идеи. С Энкост такая ситуация попросту невозможна – ведь стартовых затрат у предприятия не было, а отказаться от использования системы можно в любой момент.
4. Качественное тестирование. При работе с аналогичными системами мониторинга собственники бизнеса часто попадают в своеобразную ловушку. Оборудование стоит дорого, эффективность его неизвестна – а значит, начать использование лучше всего с одного станка, чтобы не понести слишком больших убытков в случае неудачи.
Но проверять комплексную систему на одной единице техники не имеет никакого смысла. Это как оценивать эффективность лекарства, приняв только одну таблетку из месячного курса. Конечно, в этом случае результата не будет, а потому от внедрения системы контроля производства организация откажется.
Специалисты Энкост сами спроектируют оптимальную схему мониторинга и проведут все работы по настройке оборудования, чтобы заказчик убедился в эффективности системы. Если для полноценного тестирования потребуется задействовать 50 станков – то так и будет сделано, без каких-либо затрат со стороны предприятия.
Ведь Энкост Мониторинг – сервис по подписке, а потому заинтересован в продаже результата – увеличении производительности, а не оборудования, консультаций, услуг программирования и т.д.
В заключение отметим, что Энкост – 100% российская разработка с полным иммунитетом от западных санкций.
ИНН: 7710944648
>Перекуры, опоздания и внеплановые перерывы могут легко занять до 25% рабочего времени.Трудовой кодекс вполне себе определяет период рабочего времени, а так же иные периоды приравненные к рабочему, как то перерывы которые работодатель обязан предоставлять например по причине монотонности рабочих операций (почти любой типичный станок) или неблагоприятных условий труда (почти любой типичный цех). И они могут составлять даже больше четверти рабочего времени.Но с нашей культурой взаимоотношений работодателей и работников — первые, хочешь въе хочешь уе, — вторые, летела ракета упала в болото какая зарплата такая работа — подобные опции конечно будут пользоваться спросом.
Вот, будущее уже здесь. А ведь кто-то тут заливал нам, что для таких систем обязательно сотовая связь 5G нужна, а ну как в одном цеху миллион станков соберётся? 🙂
Вспоминается история-анекдот, как было в цеху одно узкое место в перевозке продукции между цехами, выделили еще одного работника, никаких изменений не было.Пришла комиссия, оказывается у них на 3 человека одна тележка была.Поэтому контроль и понимание всех процессов очень важно ;-)Но обычно в самом цеху все и так знают, в чем дело и надо просто спросить, если работники или руководство цеха не фильтруют эту информацию в своих интересах, а этот клубок почти всегда присутствует и распутать его очень сложно.
Ух, что это у нас тут, Графана с Прометеем на производстве, занятно-занятно.В целом, по описанию — ну, неплохо. У нормальных вендоров, на автоматизированных линиях, правда, есть свои SCADA-системы, которые делают все вышеперечисленное. Но для небольших производств, которые работают "по-старинке" — почему бы и нет, наверное. Ниша золотая.
Учавствовал я во внедрении подобной системы контроля и мониторинга: данные с датчиков, инверторов собирались контроллером и отсылались на сервер, который с помощью специализированного ПО обрабатывал данные и выдавал тоже графики и статистику. Скажу одно: внедряли эту систему дольше, чем она проработала. У руководства и на местах нет понимания, как работать с этими данными. Один уровень контроля не связан с другим и данные никак не обобщаются. Вот тут как раз таки нужен ИИ, чтобы всё объединить, сопоставить и в удобоваримом виде представить, чтобы люди увидели узкие места.
Gray, Не слышал, чтобы в этих SCADA системах была возможность указать причину простоя линии, могу ошибаться конечно.
iAndroid, Один из быстрых эффектов от внедрения — это как раз прозрачность. Понятно, когда и по какой причине был простой, не получится фильтровать информацию в чьих-то интересах.
GrishaTav_SE, Вот-вот, 2G хватило с запасом)
мимoпроходил, По нашему опыту, ситуация, когда работодатель дорожит квалифицированными работниками — скорее правило, чем исключение. Хотя может это и "ошибка выжившего" — всё-таки мониторинг заказывают предприятия загруженные заказами, а значит испытывающие проблемы с нехваткой станочного времени, а не денег на ЗП.
EncostMonitoring, Там, как правило, из алерта причина понятна. Автоматизированная линия же. Но наколхозить кнопку с выборами причины — прям задача максимально тривиальная. Api там, все дела. P.S. Если вы наколхозить свою СКАДУ, которая будет совместима с большинством популярных китайских станков, будет иметь централизованное управление, очень продвинутый алертинг (аля тот же OpsGenie), для промки это будет прям сильвербуллет. Вам не нужно такое количество киповцев/операторов, когда сама система — они и есть.
Kharkov-city, Мы всё-таки следим за станками на загруженных заказами производствах (а другим мониторинг и не нужен, зачем платить за мониторинг если и так понятно, что станки стоят без сменного задания). Вы наверное описываете кейс из серии: "сотрудник на заводе всегда должен быть чем-то занят, неважно чем…" — это да, до добра не доводит, согласен.
izzzgoy, Бывает, что нет понимания, как работать с данными — тут Вы абсолютно правы. Мы решаем эти проблему в двух направлениях: во-первых добиваемся, чтобы был назначен ответственный за работу с системой (это и есть наш ИИ), во вторых мы делимся с клиентами лучшими практиками других клиентов (тут понятно, что с нами не всем делятся, но кое-что знаем).
Gray, За 4 года работы по оценке самой компании ЭНКОСТ, заказчики сэкономили около полу-миллиарда рублей на покупке нового оборудования. А объем дополнительной продукции, произведенной за счет возросшей производительности, оценивается в те же 500 миллионов рублей, но уже ежегодно.
"На каждый станок крепится смартфон с настроенным телеграм-ботом" "В заключение отметим, что Энкост – 100% российская разработка с полным иммунитетом от западных санкций." — серьёзно с иммунитетом? Мониторинг данных предприятия передающихся через иностранную соц-сеть, ключи шифрования которой она передала АНБ США, находящуюся в недружественной юрисдикции с возможностью отключения в любой момент, странный иммунитет. Просто прелестно.