Привет.
Каждый человек, имеющий возможность часто посещать производство электроники, невольно проходит внутреннюю эволюцию. От восторга познания нового к позевыванию в последующие разы, а затем к пониманию мелких деталей, отличающих одну компанию от другой. Такие детали выпирают на любом производстве, нужно уметь их подмечать и задавать вопросы, ответы на которые дополняют общую картину.
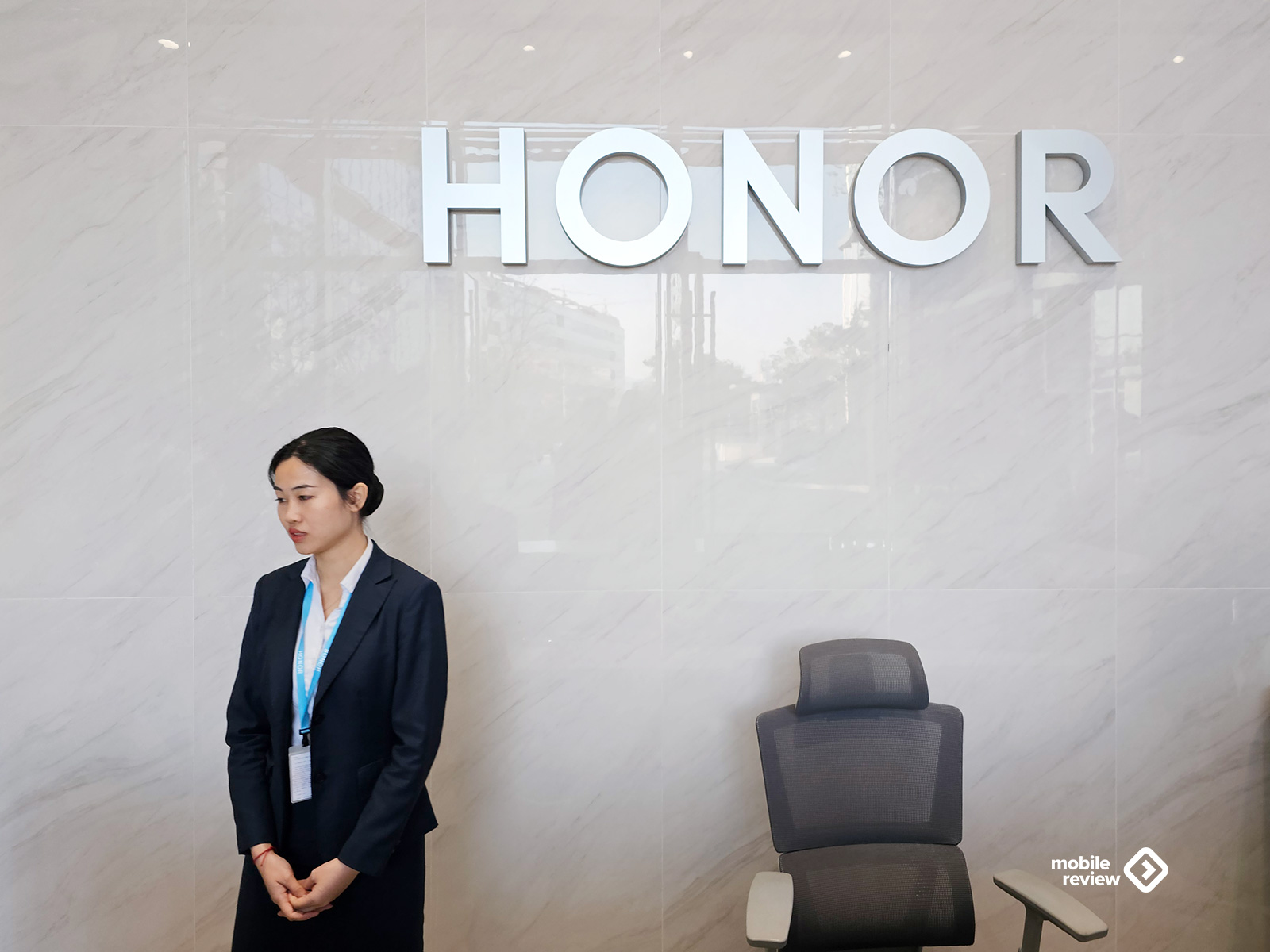
В Honor организовали поездку в исследовательский центр компании, в лаборатории, где испытывают устройства, а также непосредственно на производство. За пару месяцев до этого был на заводе OPPO, а также в лабораториях, где разрешили без ограничений фотографировать и снимать видео, что для таких мест дело неслыханное. В Honor в деталях все показывали, но фотографировать не давали, на входе нужно было сдать все устройства, их складывали в отдельный ящик.
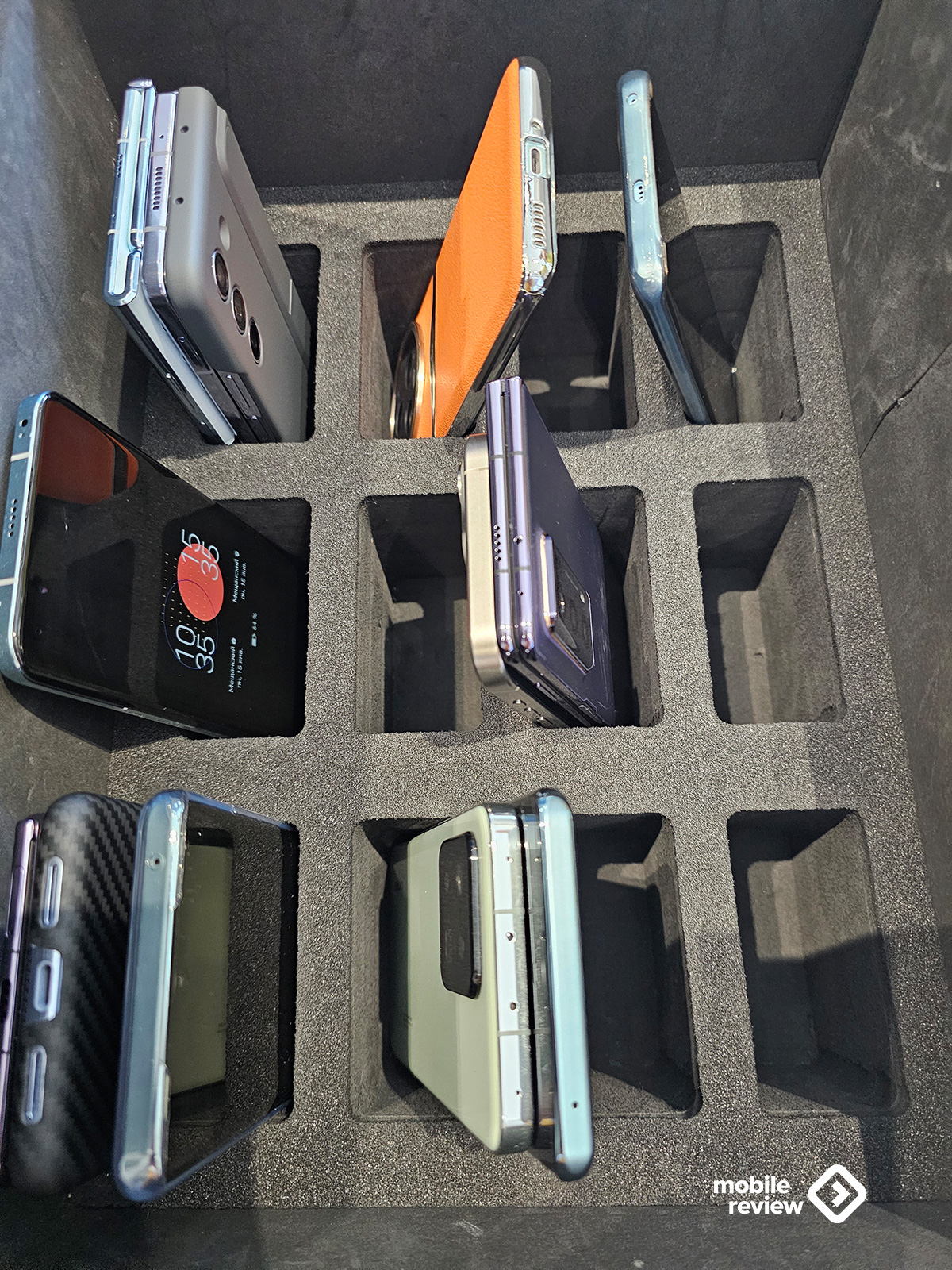
Поэтому фотографии, которые вы увидите ниже, предоставлены самой компанией, кое-какие этапы производства отсутствуют, нет важных мелочей. С другой стороны, никто не мешает нам обсудить все особенности производства, труда рабочих на конвейере и в цехах.
Путешествие до большого индустриального парка начинается из центра Шэнчьжэня, огромный мегаполис постоянно перестраивается и уже обогнал многие города мира по репутации, он воспринимается как центр инноваций в Китае. Для страны это визитная карточка, которая показывает все самое-самое, а для производителей электроники — удобный хаб, который рано или поздно сместит с первых строчек Тайвань. Амбиции таковы, что Китай станет производителем полного цикла, от компонентов до конечных устройств. Плюс Шэнчьжэня также в отличной логистике, готовые товары могут доставляться в любую точку мира как морем, так и самолетами, равно как работают и обратные маршруты для поставок материалов, необходимых для производства.
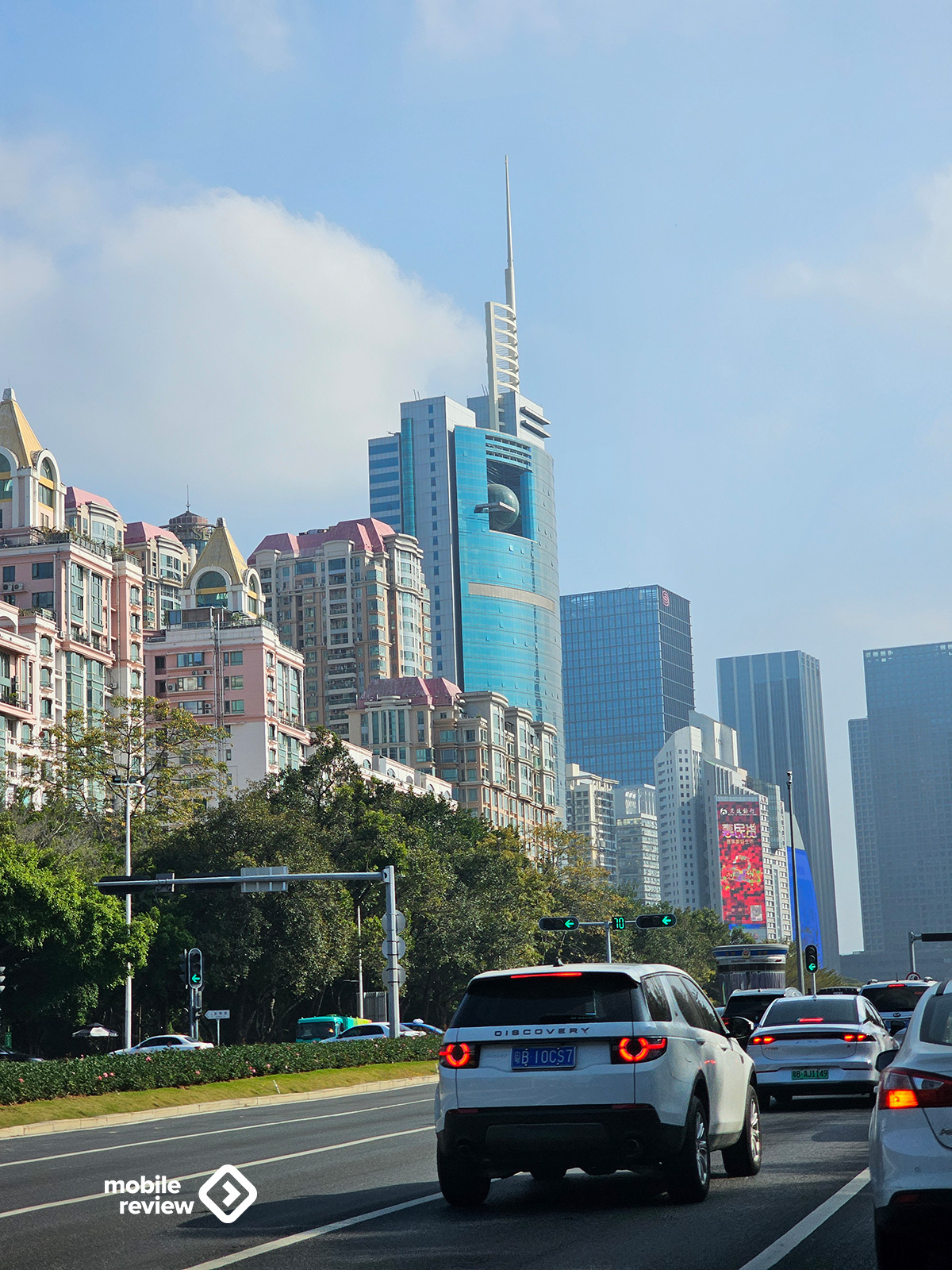
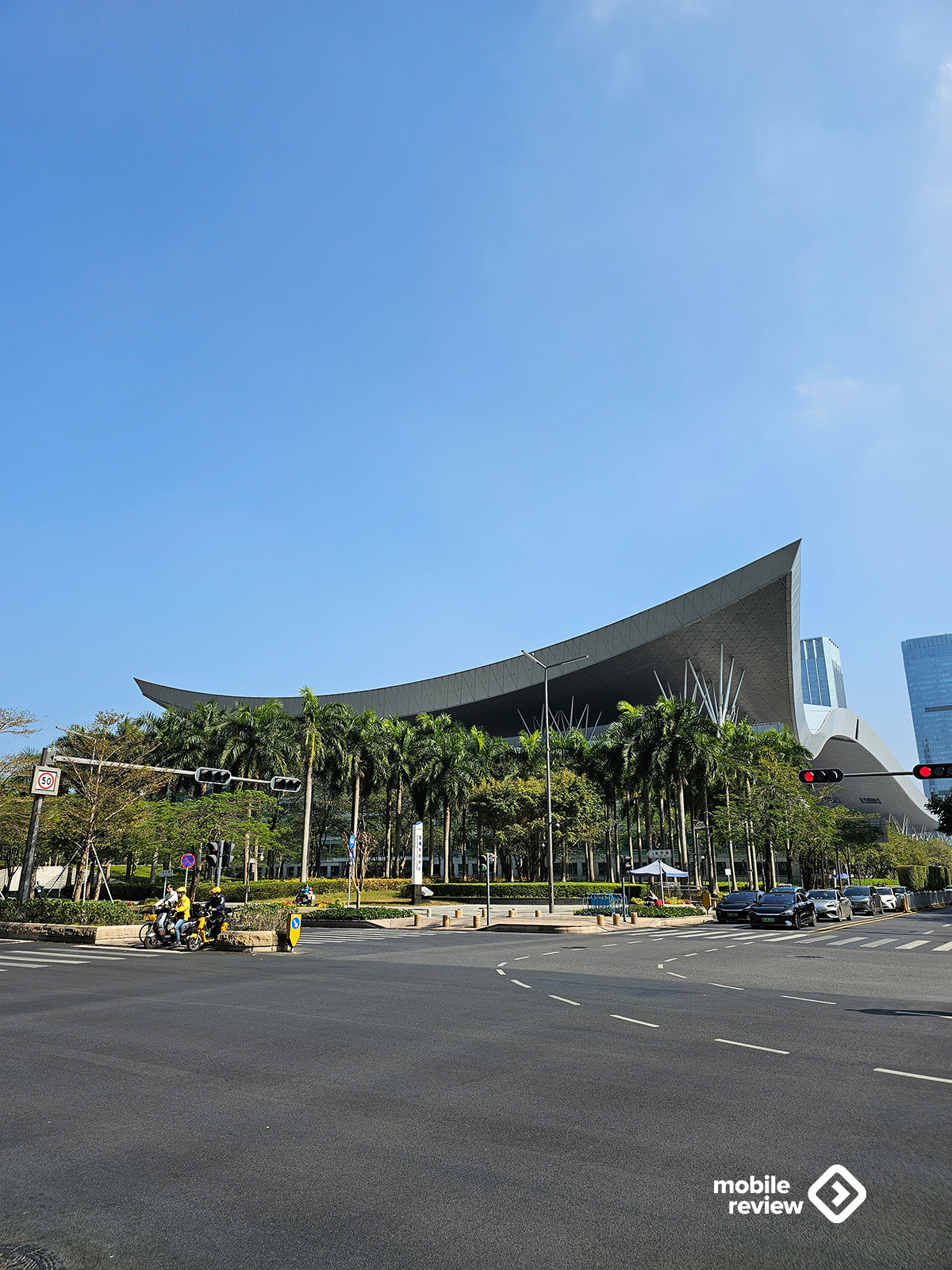
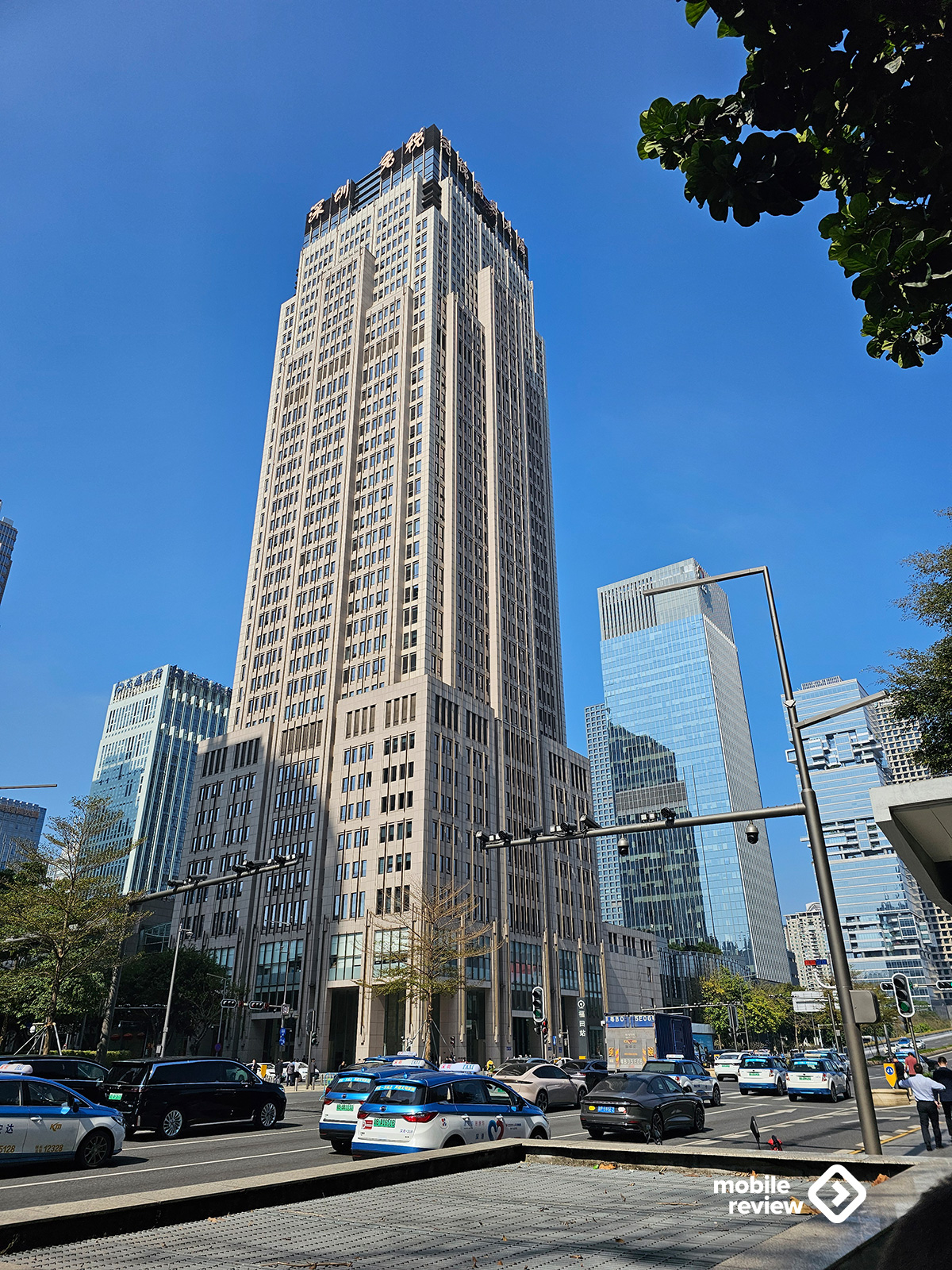
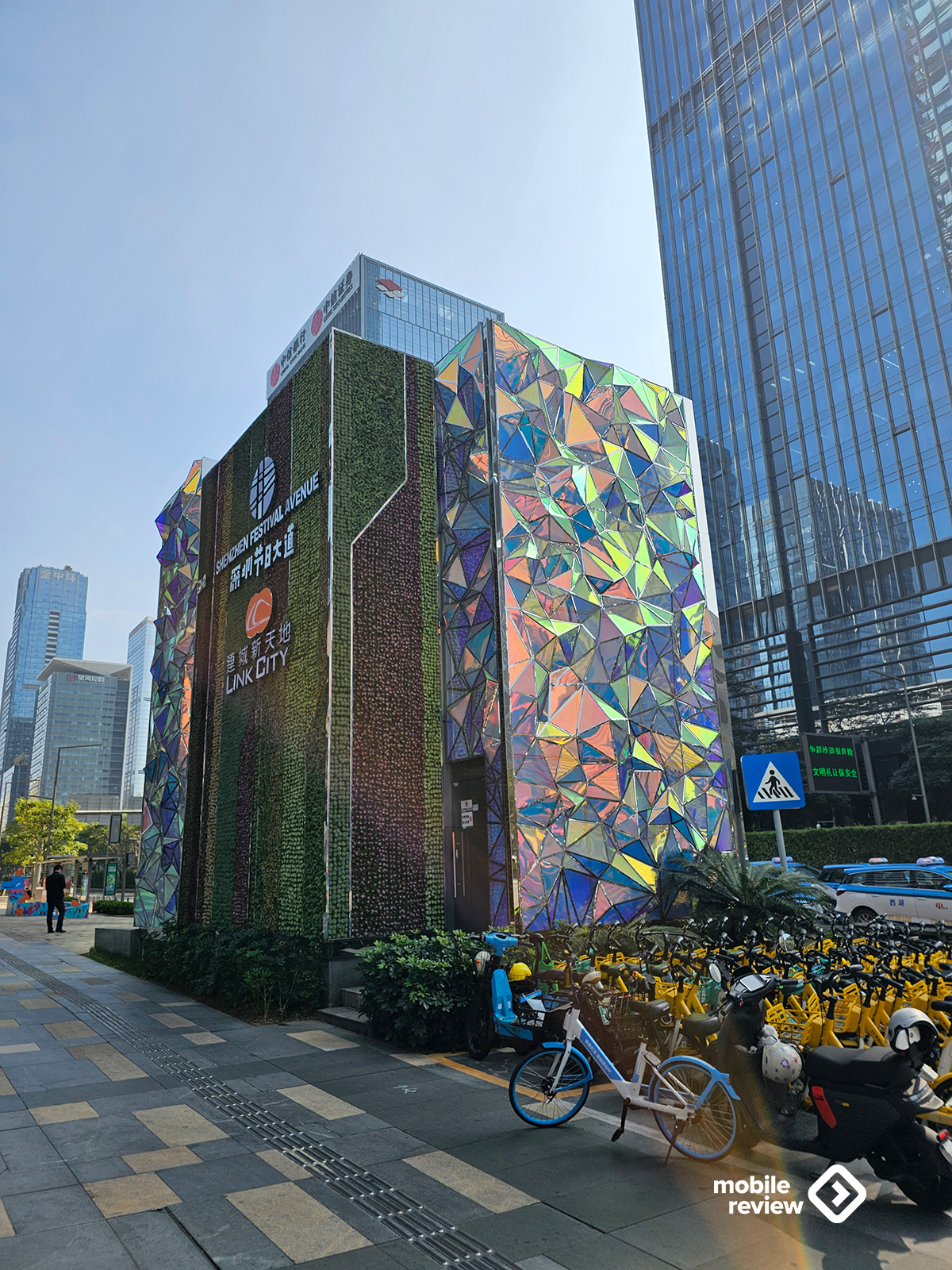
После того, как Huawei продала Honor и компания стала независимой, встал насущный вопрос того, что для нее необходимы новые пространства для центра разработок, производственных линий. Шэнчьжэнь предоставил место для строительства фабрики и дополнительных корпусов, где размещаются исследовательские лаборатории, офисные пространства и склад. Автобус едет по дороге, с другой стороны видны разрушенные здания, строительный мусор затянут зеленой сеткой — привычная для Китая картина, так пытаются украсить пространство. Вдоль дороги протянулись огромные постройки, кое-какие уже готовы наполовину, какие-то только начали возводить. Насчитал больше десятка зданий, не считая такого же количества котлованов или площадок. Спрашиваю у нашего сопровождающего, чьи это пространства, кто тут строится. Ответ меня удивляет — через дорогу идет строительство цехов Huawei. Бесконечная череда зданий, которые через года полтора-два превратятся в суперсовременный город-завод, вбирающий в себя кучу разных функций. Уверен, что мимолетно брошенная фраза про Huawei как-то отозвалась у нашего китайского товарища, но для меня это зримое отображение концентрации компаний в одном месте.
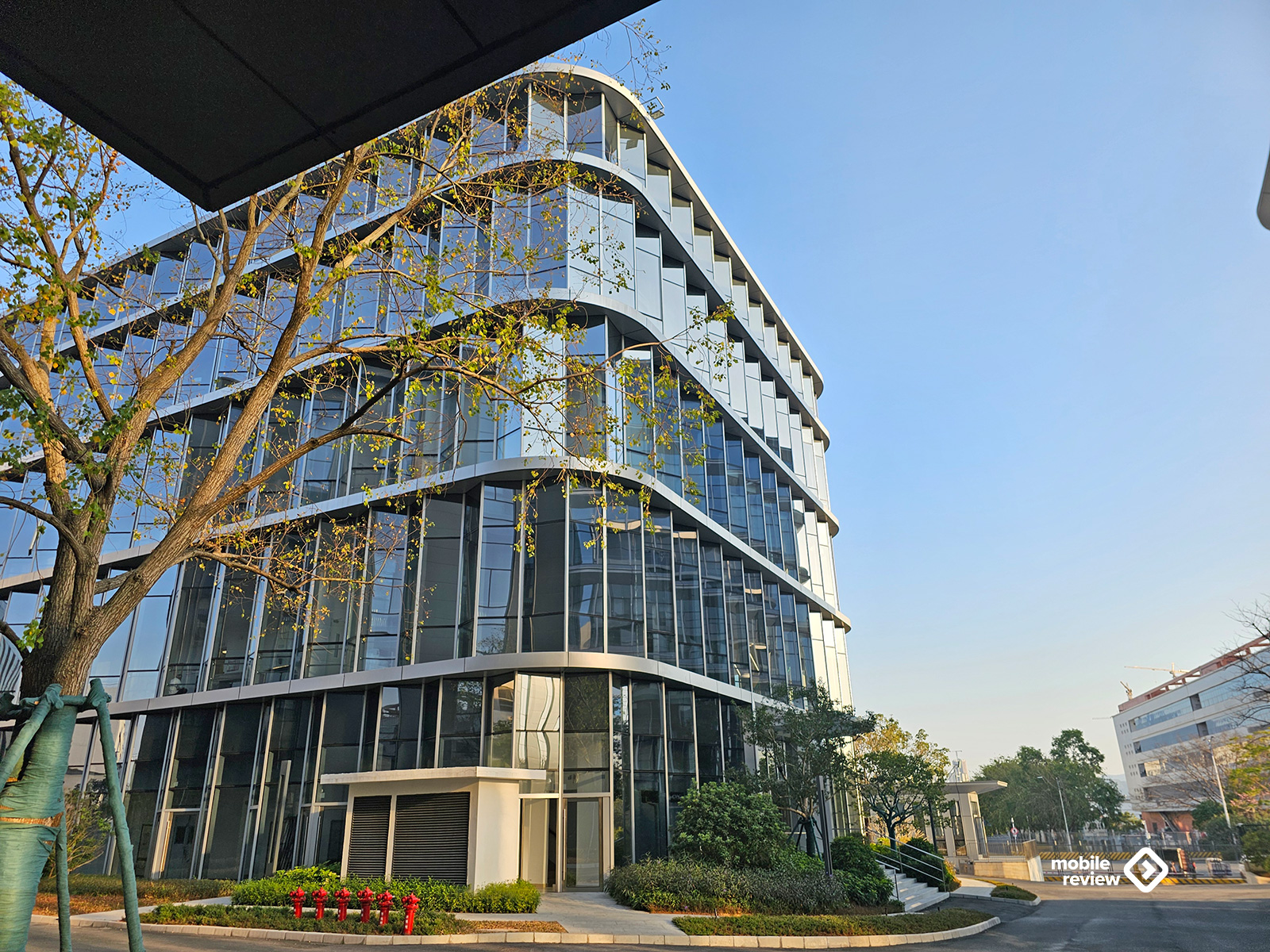
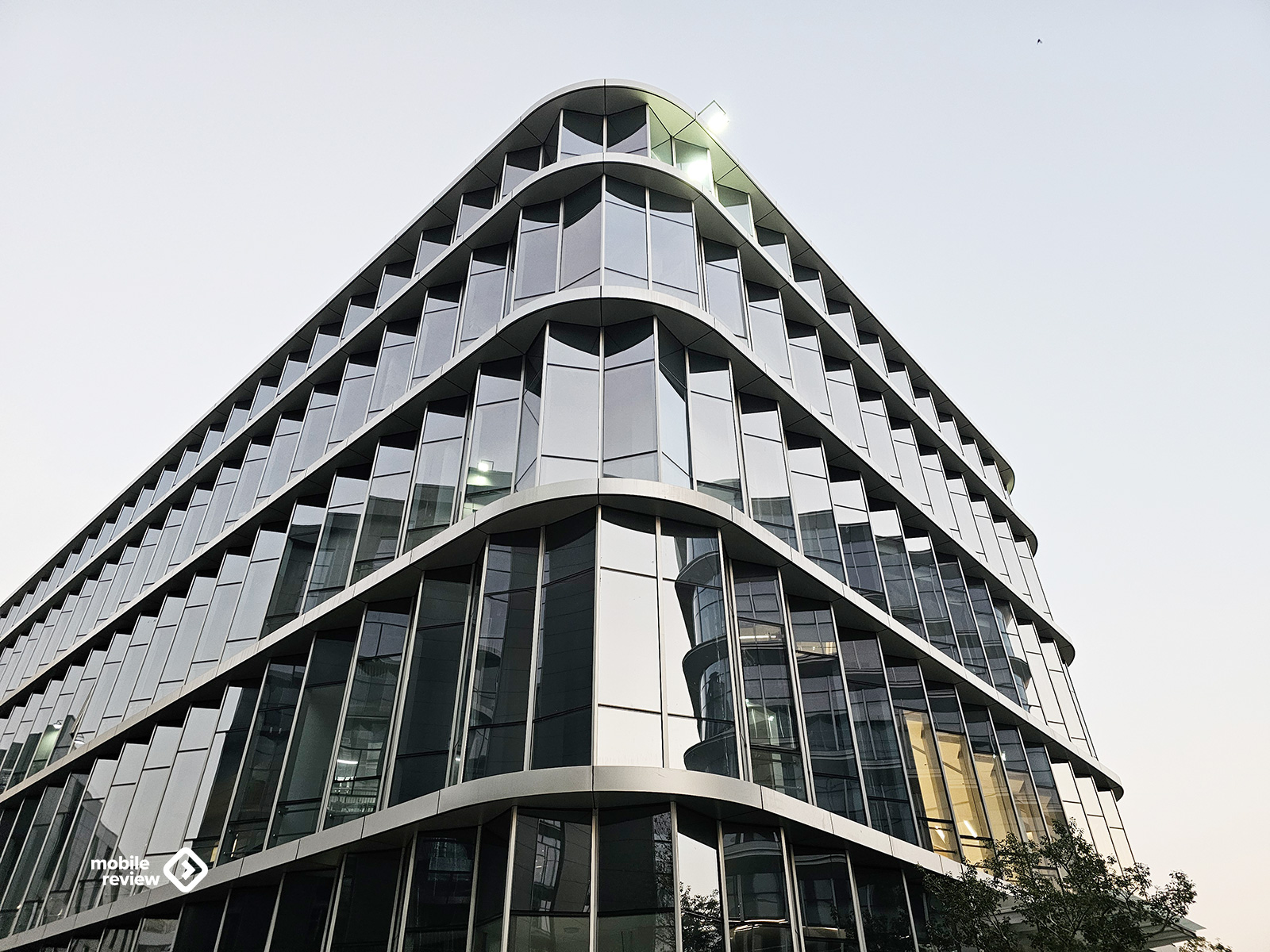
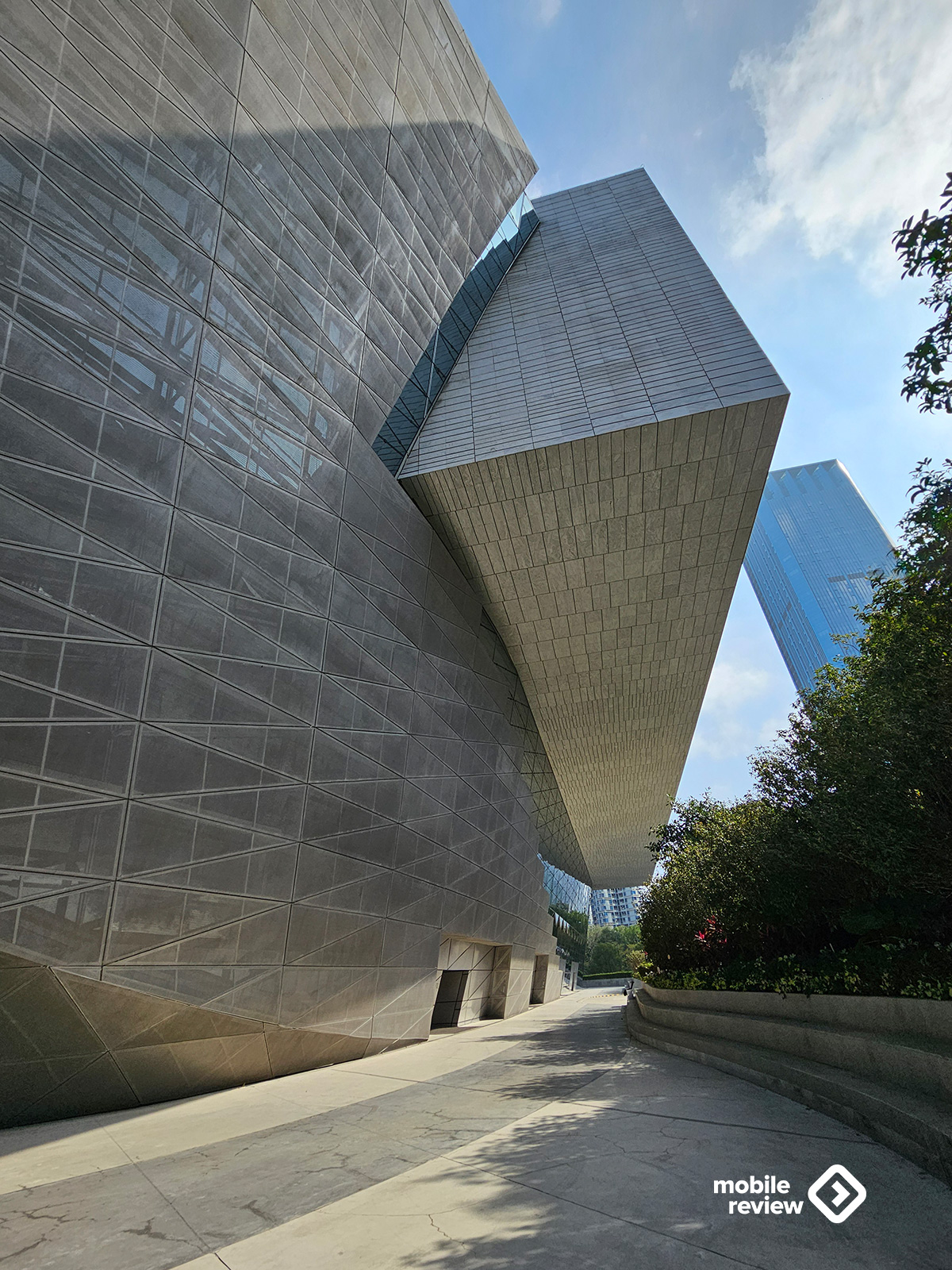
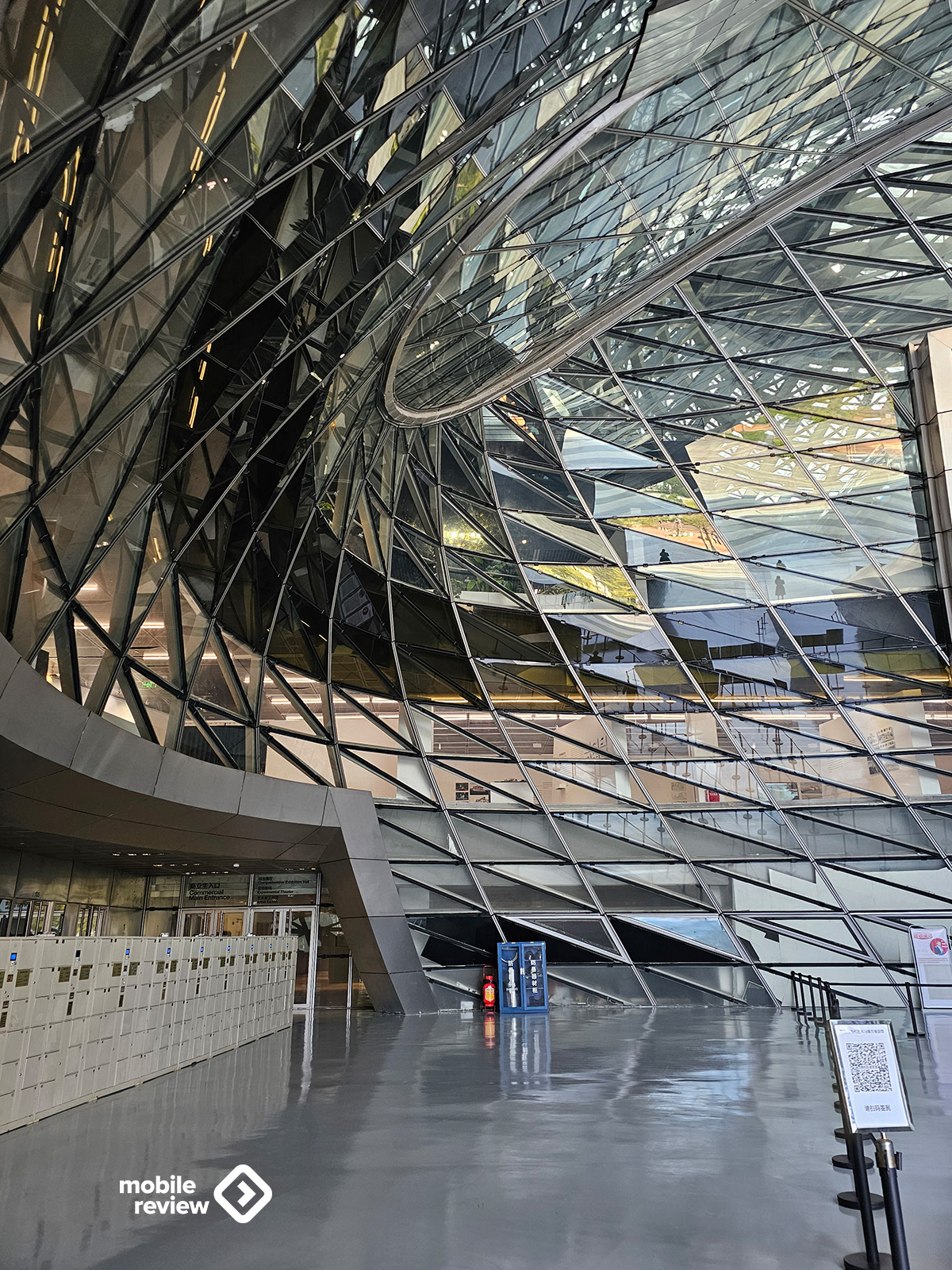
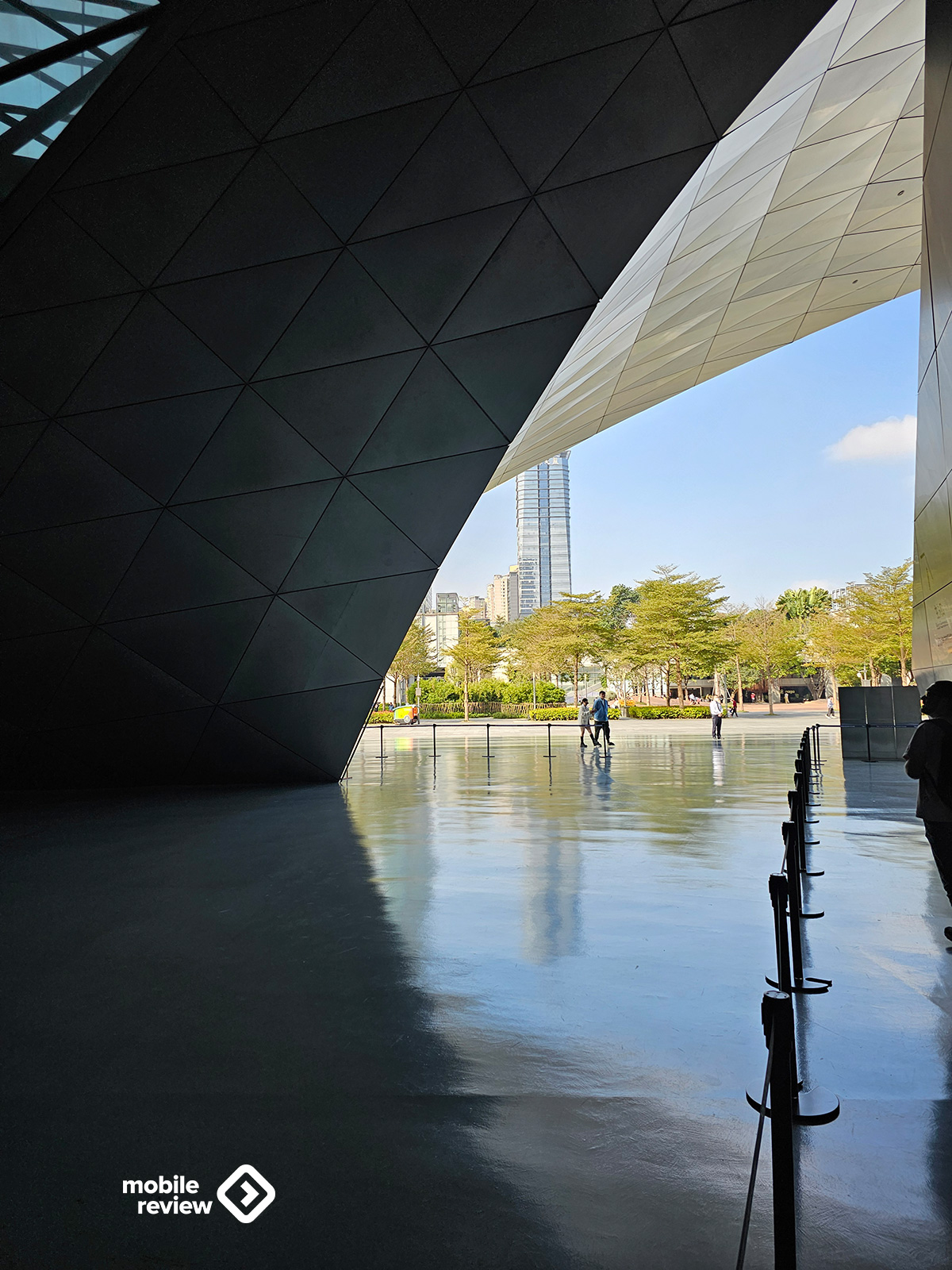
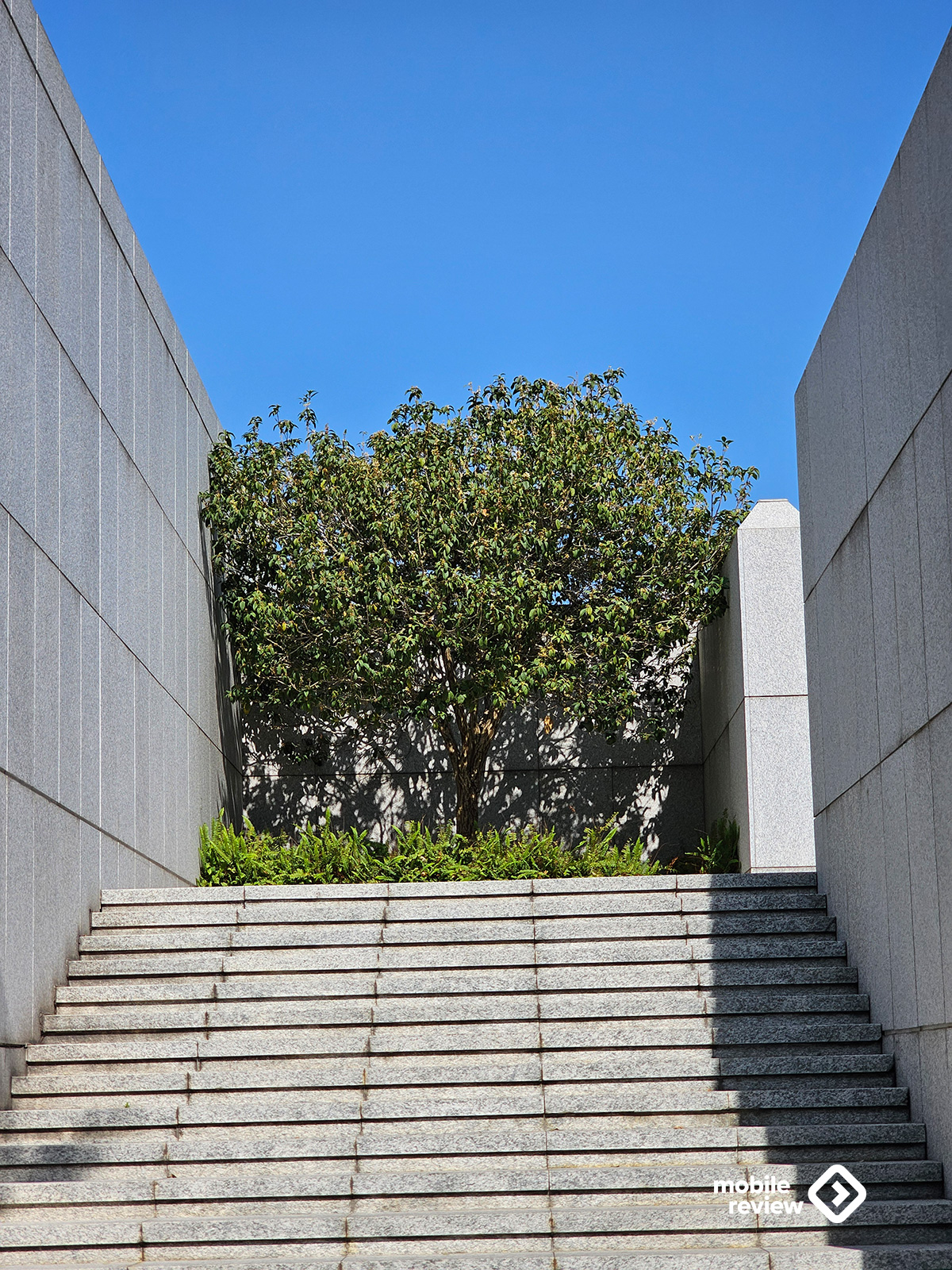
В Honor за год с небольшим построили подобное место и назвали его HONOR Intelligent Manufacturing Industrial Park (то есть объединили в одном месте все возможные функции современного производства электроники). Получается, что вокруг индустриального парка Honor раскинется Huawei, давшая когда-то жизнь этому бренду, а потом уже и отдельной компании.

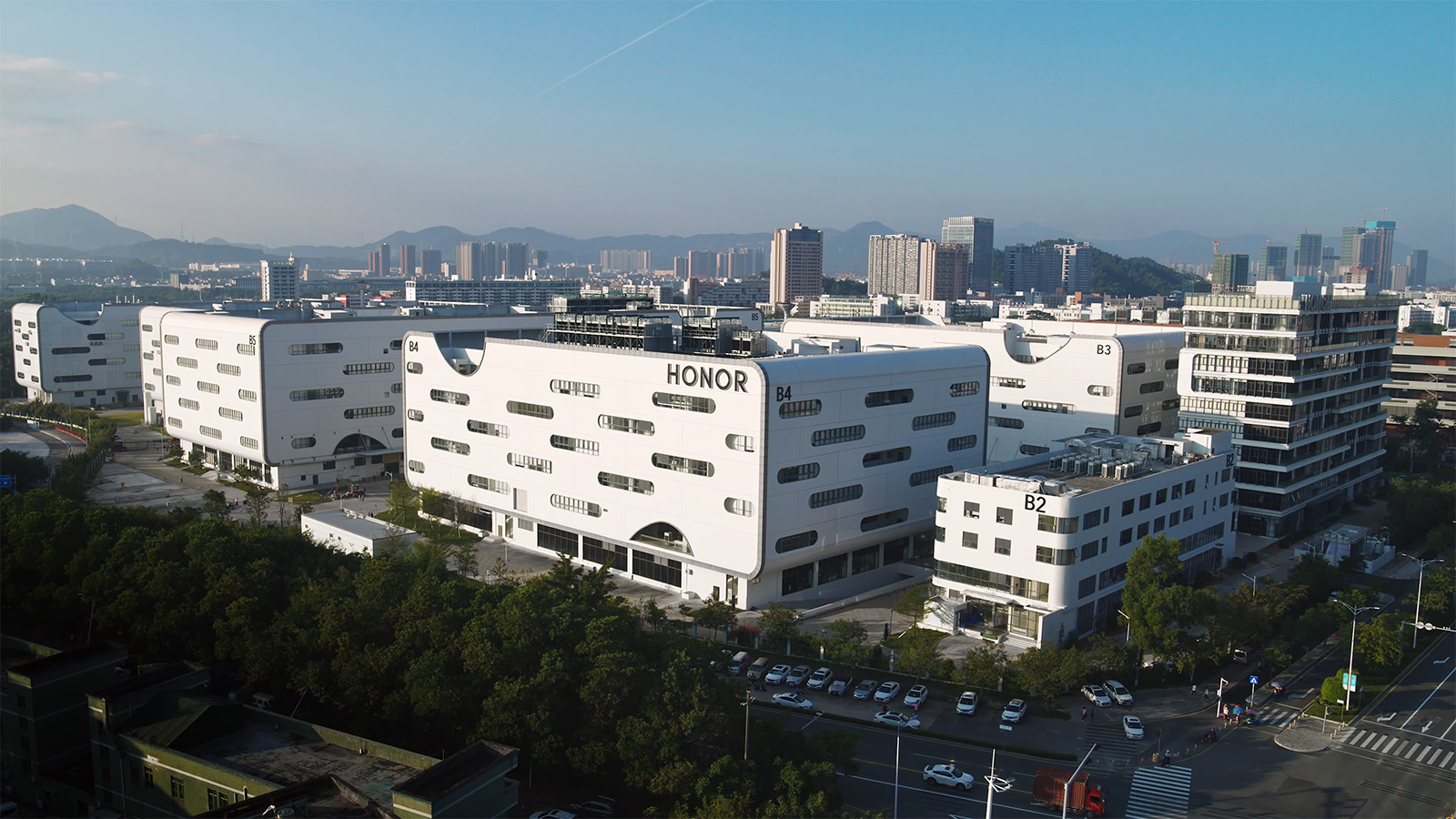
Снаружи можно фотографировать, так что делаю снимки зданий, они разделены идеологически: производство в одних зданиях, R&D — в других, офисы — в третьих. Нас ведут на производство, но вначале нужно облачиться в халаты и шапочки, они необходимы, чтобы избежать любой статики.
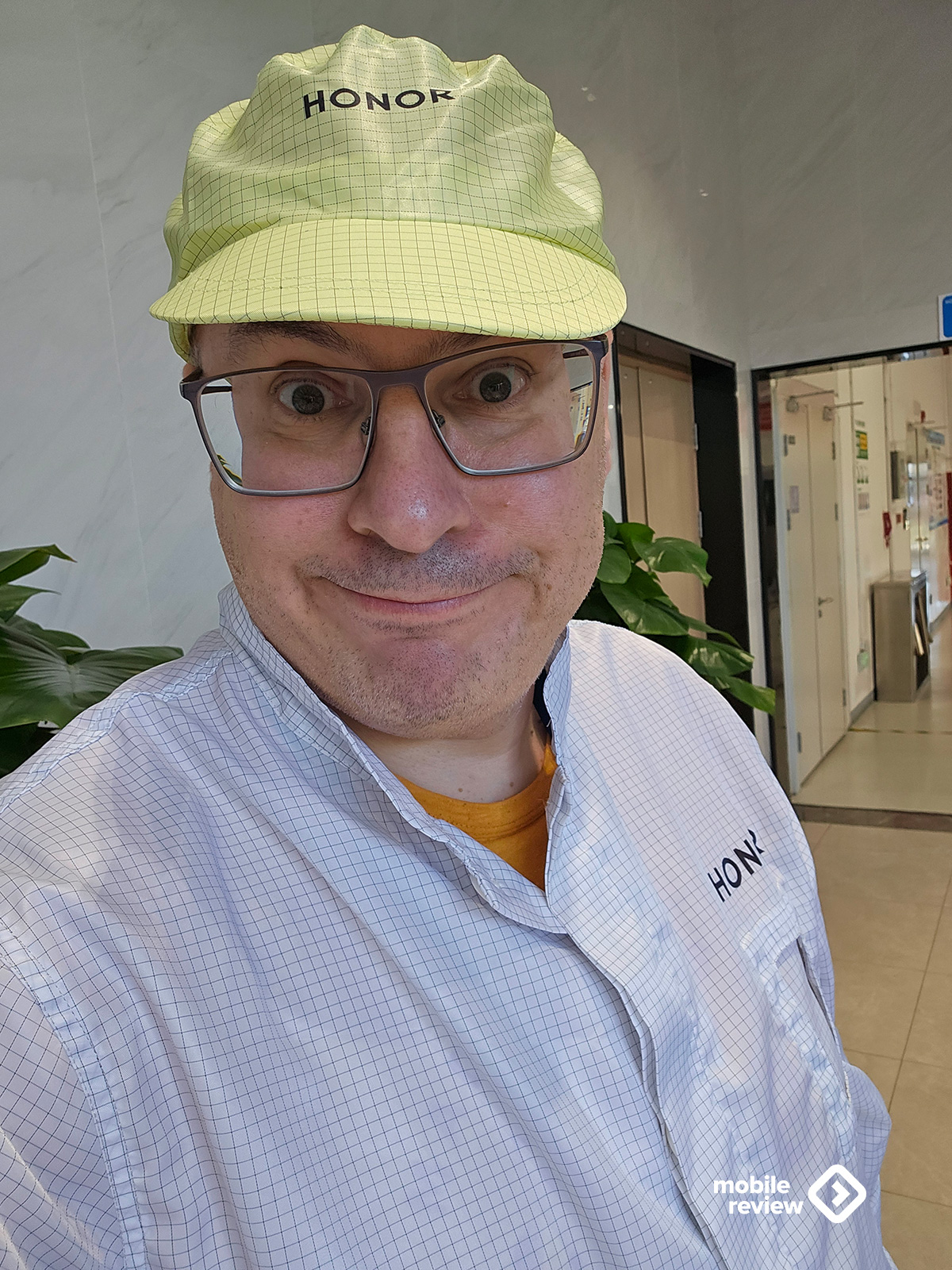
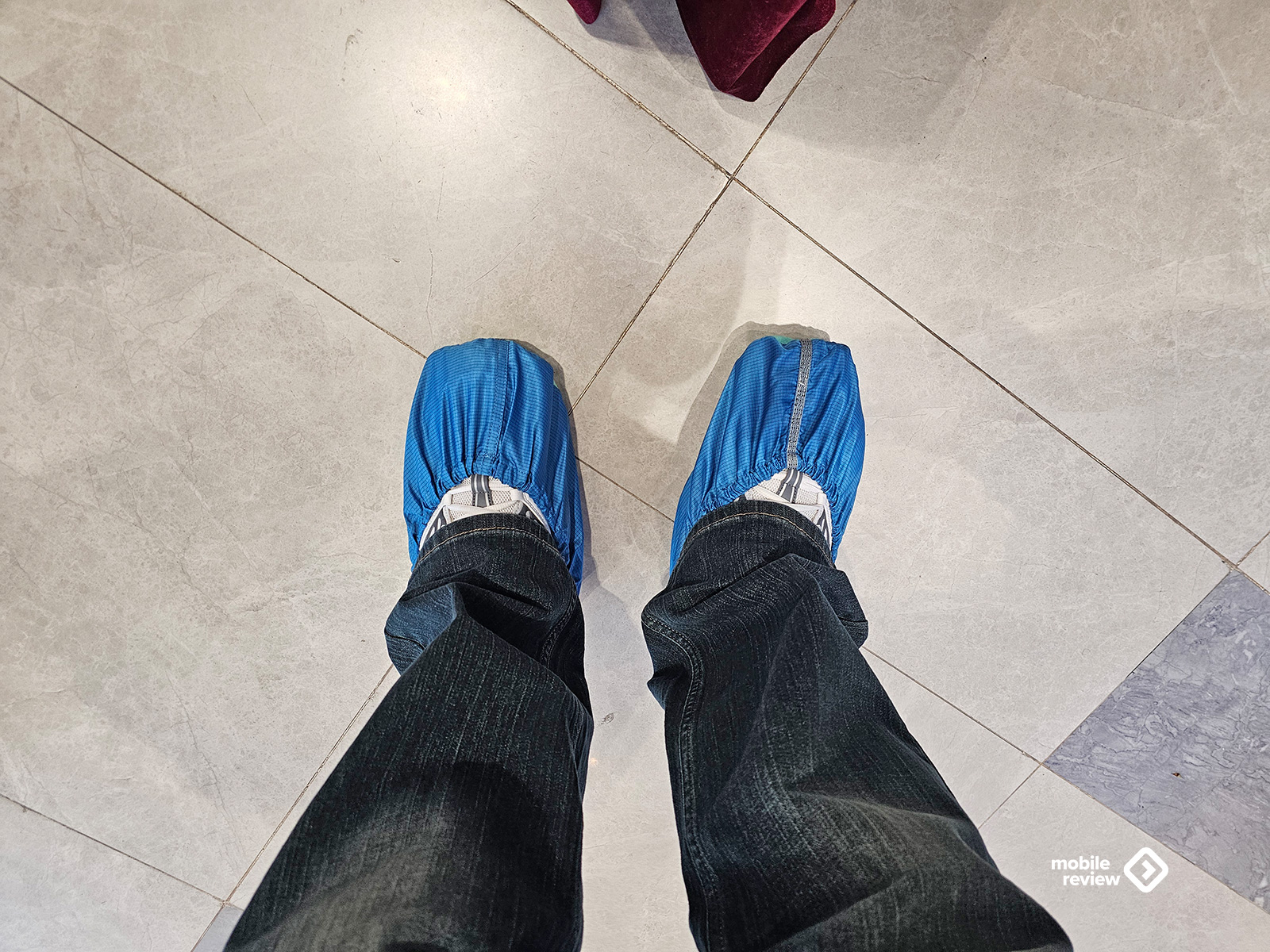
Производство располагается в отдельном корпусе, оно начало работать в ноябре 2021 года. Для меня это самый свежий завод из всех, что я посетил за последнее время. Свежесть завода важна, так как она позволяет использовать последние наработки, и мы видим на производственных линиях те или иные ноу-хау, которые отсутствуют на старых линиях. Короткая презентация, в которой рассказывают про производственные линии, наполнена цифрами из пресс-релиза ноября 2021 года: «Линия выдает один смартфон каждые 28.5 секунд», «рабочий получает на производстве в среднем на 40% больше, чем в индустрии». Когда-то согласованные цифры остались неизменными, хотя за пару лет производство изменилось и многие показатели улучшились или просто стали иными, но про это сопровождающий инженер говорить не может. Приходится мучить его дополнительными «невинными» вопросами, которые позволяют рассчитать емкость производства, его скорость и другие параметры. Инженеру льстит, что его спрашивают о деталях его работы, о том, что практически никого и никогда не интересует. Он рассказывает, как выглядит склад компонентов, как часто их приходится менять, как работают смены на заводе и далее по списку. Постепенно цифры из пресс-релиза уходят в сторону, и вырисовывается реальная картина производства.
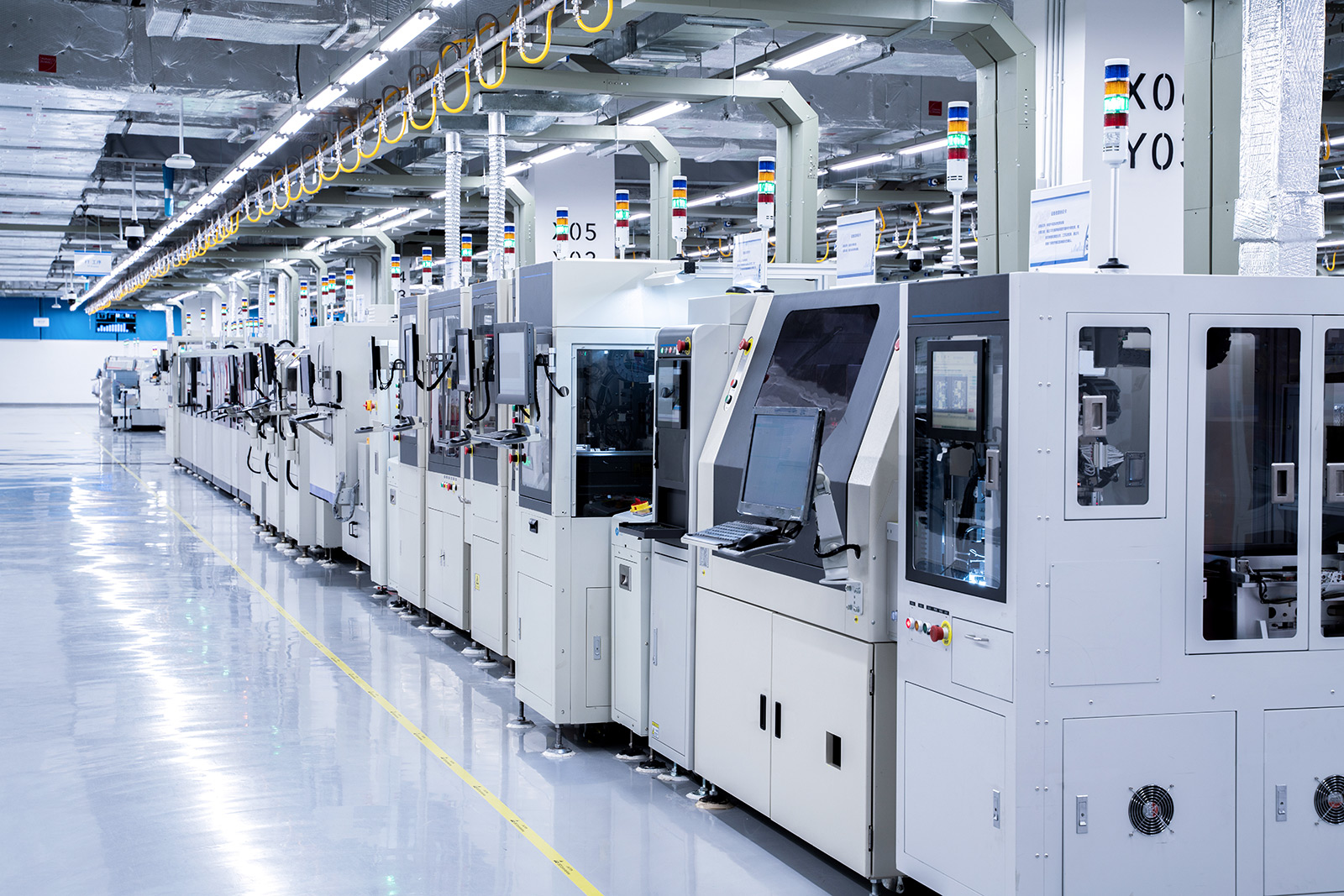
Мы идем вдоль первой SMT-линии, которая собирает платы и затем устройства. Всего их больше двух десятков, но точное число является коммерческой тайной. Думаю, что не ошибусь, если скажу, что их может быть до трех десятков, строилось производство с размахом и для того, чтобы иметь возможность максимально быстро увеличивать число производимых телефонов, в том числе сложных, с гибким экраном. В момент посещения завода на нем производили Honor Magic6 Pro, а среди моделей с гибким экраном отмечу Honor Magic V2.
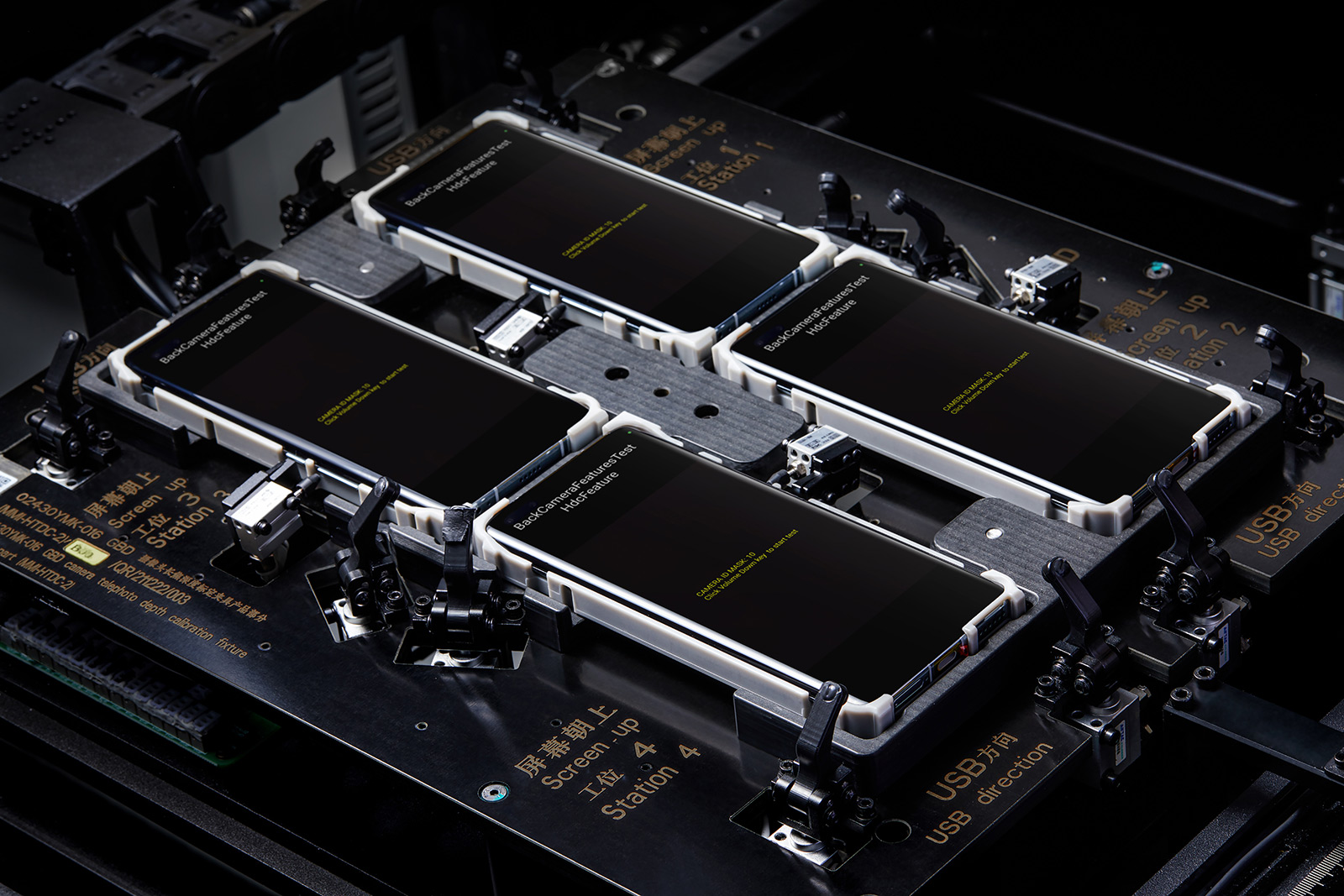
Разные машины выстроены в одну линию, на столбах здания видны обозначения, как на парковках в торговых центрах или в аэропортах, они позволяют рабочим ориентироваться. У каждого номера столба стоят свои машины одного типа, фактически каждая производственная линия повторяет соседнюю, сделано это с умыслом — чем больше стандартизации, тем лучше. Длина линии — 149 метров. На момент открытия производства одну линию обслуживали 24 рабочих, уровень автоматизации составлял 75%. В январе 2024 года число рабочих сократилось до 20, уровень автоматизации достиг почти 83%. Это важный показатель, демонстрирующий желание компании максимально сократить вмешательство человека, сделать линии автоматическими. И у Honor производственные линии являются произведением инженерного искусства, хотя собраны они из разрозненных компонентов. В компании гордо говорят о том, что создают оборудование самостоятельно, на многих агрегатах видна надпись Honor или аббревиатура, обозначающая автоматизированную систему управления производством. Четыре буквы HIEP расшифровываются как Honor Intellegent Equipment Platform.
Это одновременно так и не так, ведь отдельные машины производятся другими компаниями, а вот объединены они вместе IT-системой от Honor, это и правда разработка компании. Такой подход у многих производств, это единственный путь развития, позволяющий дотошно контролировать каждый этап.
Что такое автоматизация производства и какое место в этом процессе занимает человек? Рабочие работают по сменам, живут тут же в общежитии или неподалеку, второй вариант встречается очень редко. Смена длится восемь часов, в периоды высокой загрузки она может расширяться на несколько часов, на производстве Honor говорят, что это обычно до двух дополнительных часов. Каждые два часа рабочий получает перерыв на десять минут.
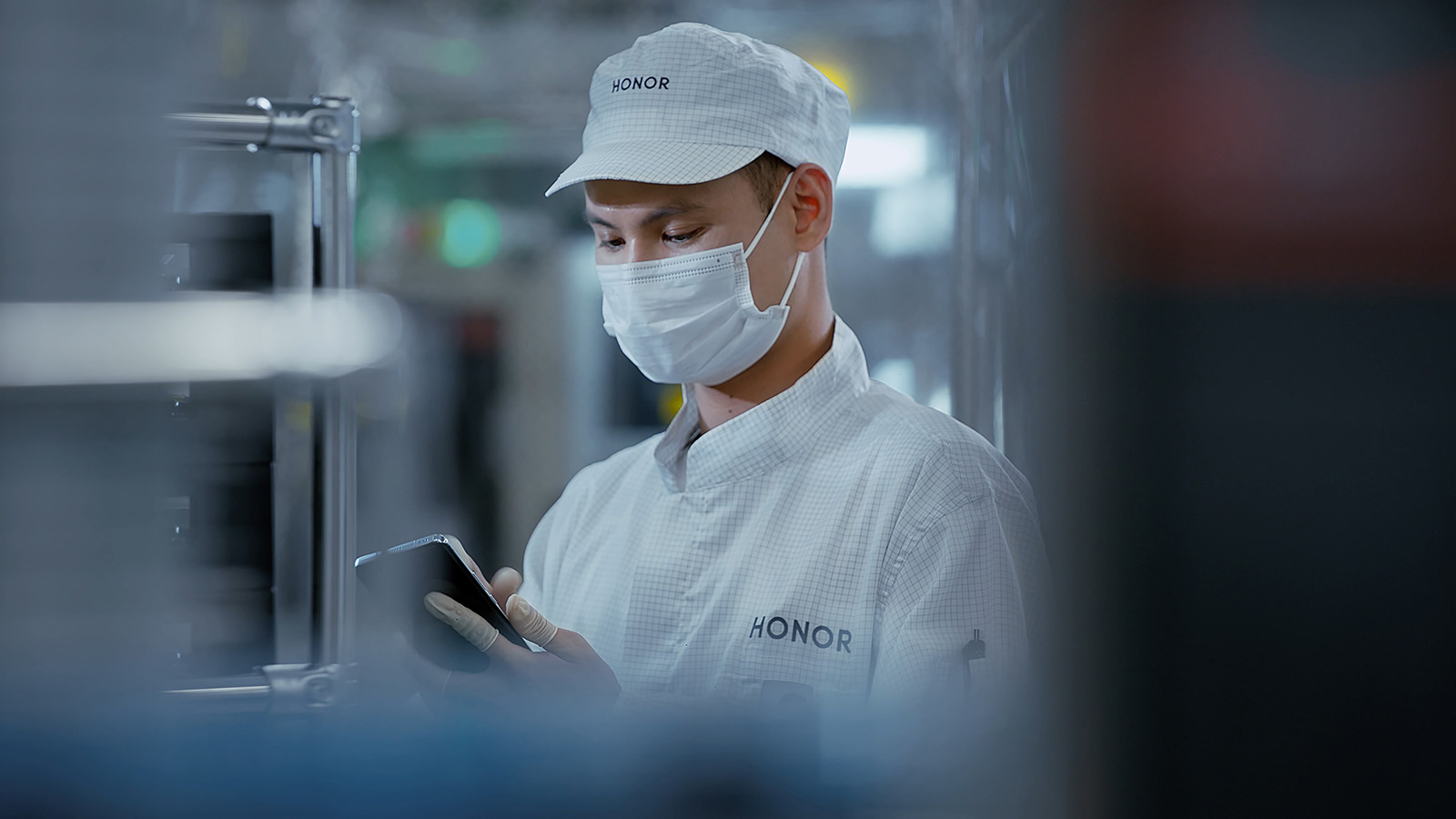
Конвейер автоматизирован, но труд рабочих монотонен. Всего их на предприятии около 5000 человек. На линиях сборки работает небольшая их часть, так как они автоматизированы (мои расчеты показывают, что от силы тысяча человек).
Каждая машина оснащена компьютерным зрением, что позволяет не только «видеть» компоненты, плату и устройство, но также контролировать путешествие заготовки по производственной линии. За скобками остается первичный контроль компонентов от поставщиков, их проверяют до того, как пустить на линию, ведь даже малейший брак в незначительном компоненте потребует переработки собранного целиком или частично устройства. Отсюда драконовские меры по контролю, отличающие Honor, тут в прямом смысле стараются контролировать все и вся. И, более того, у каждой ошибки всегда есть имя и фамилия, все ходы записаны.
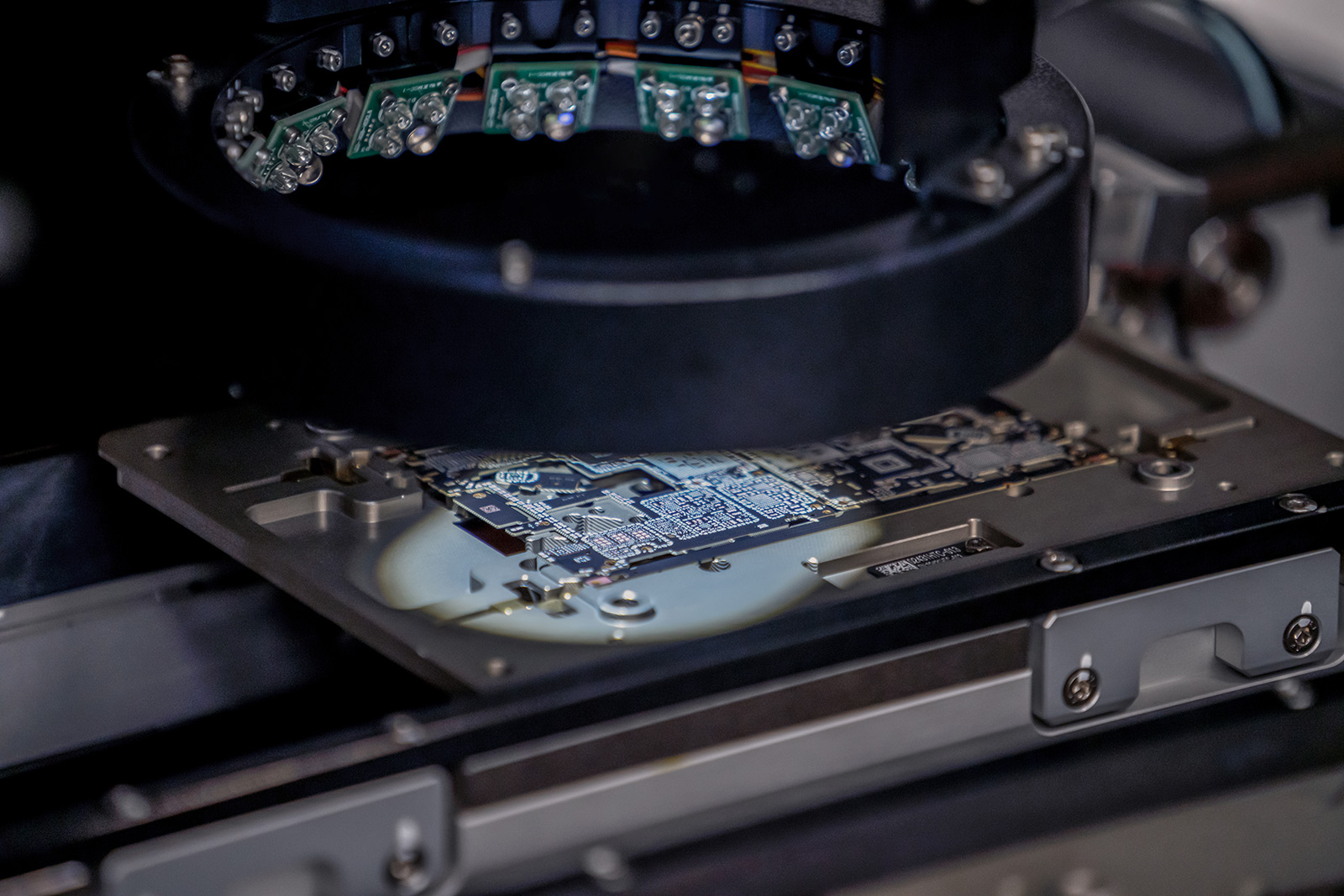
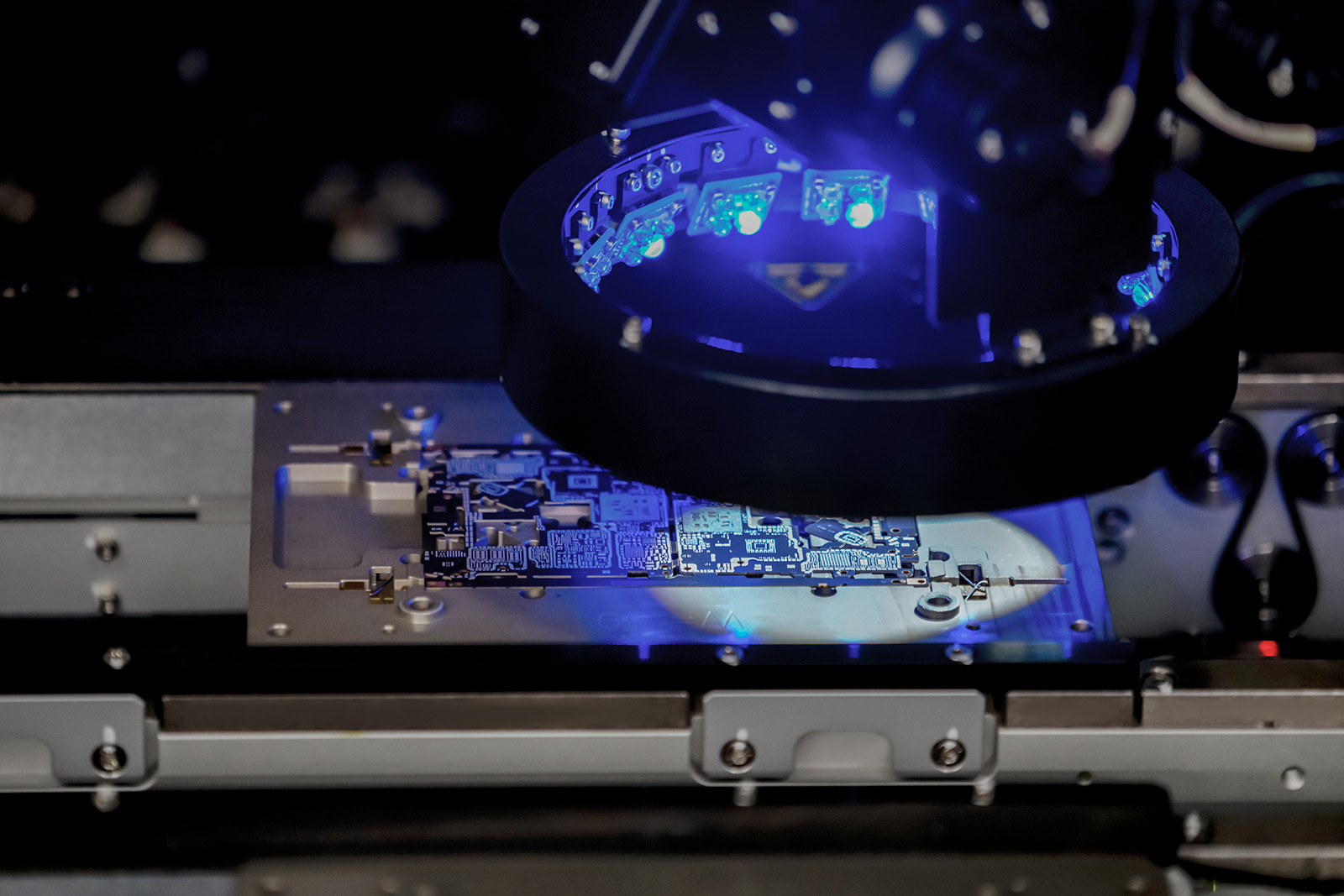
Заготовка платы поступает на линию, ее подвозят рабочие в специальных ящиках. Платы еще не разрезаны, но их контролирует специальный автомат, проверяет через камеру отсутствие брака, который можно увидеть с помощью оптики. Процент отбраковки минимален, его почти нет — ведь платы проверяли на предыдущем этапе, это перестраховка на случай, если на пути от склада до производственной линии что-то могло произойти. Далее на плату лазером наносят QR-код, рассмотреть его невооруженным глазом невозможно, нужно будет использовать лупу, а заодно знать, где его искать. Наличие QR-кода необходимо для того, чтобы проследить путь конкретной платы и далее устройства. На конвейере все фиксируется, постоянно делаются фотографии каждого устройства, все эти данные отправляются в большой дата-центр, который расположен здесь же и занимает целый этаж здания. Нам говорят о том, что он используется для разработки устройств, моделирования, но я точно знаю, что он также хранит всю историю производства.
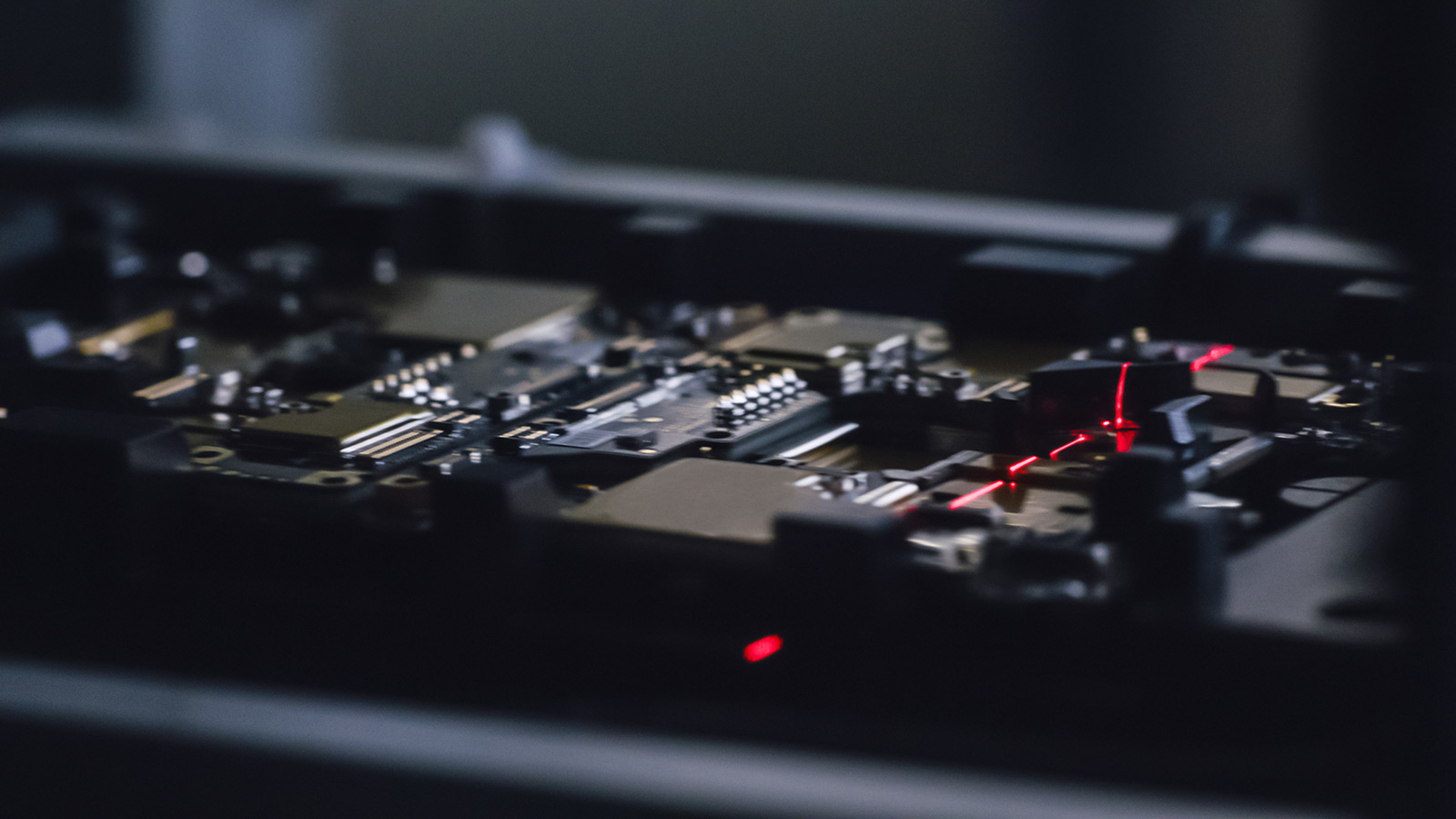
И в момент, когда пользователь где-то за тысячи километров приносит свой аппарат в сервис, компании доступна вся информация о его производстве, можно отследить каждый этап. И если случился какой-то брак, который повторяется из раза в раз, его можно отследить на уровне конкретной машины или конкретной повторяющейся ошибки. На данный момент такого, правда, не было, массовый брак при подобном подходе крайне маловероятен, и это отличает крупных производителей от небольших фабрик, они тратятся на контроль качества, причем даже не двойной, а многократный.
Никакие сложные операции не доверяются рабочим, машины на конвейере паяют детали, проверяют качество пайки, включают и выключают смартфоны, чтобы проверить их работу. Новизна линий от Honor характеризуется тем, что много роботизированных рук, они летают внутри огороженных пространств и молниеносно заменяют идущие по конвейеру платы и телефоны.
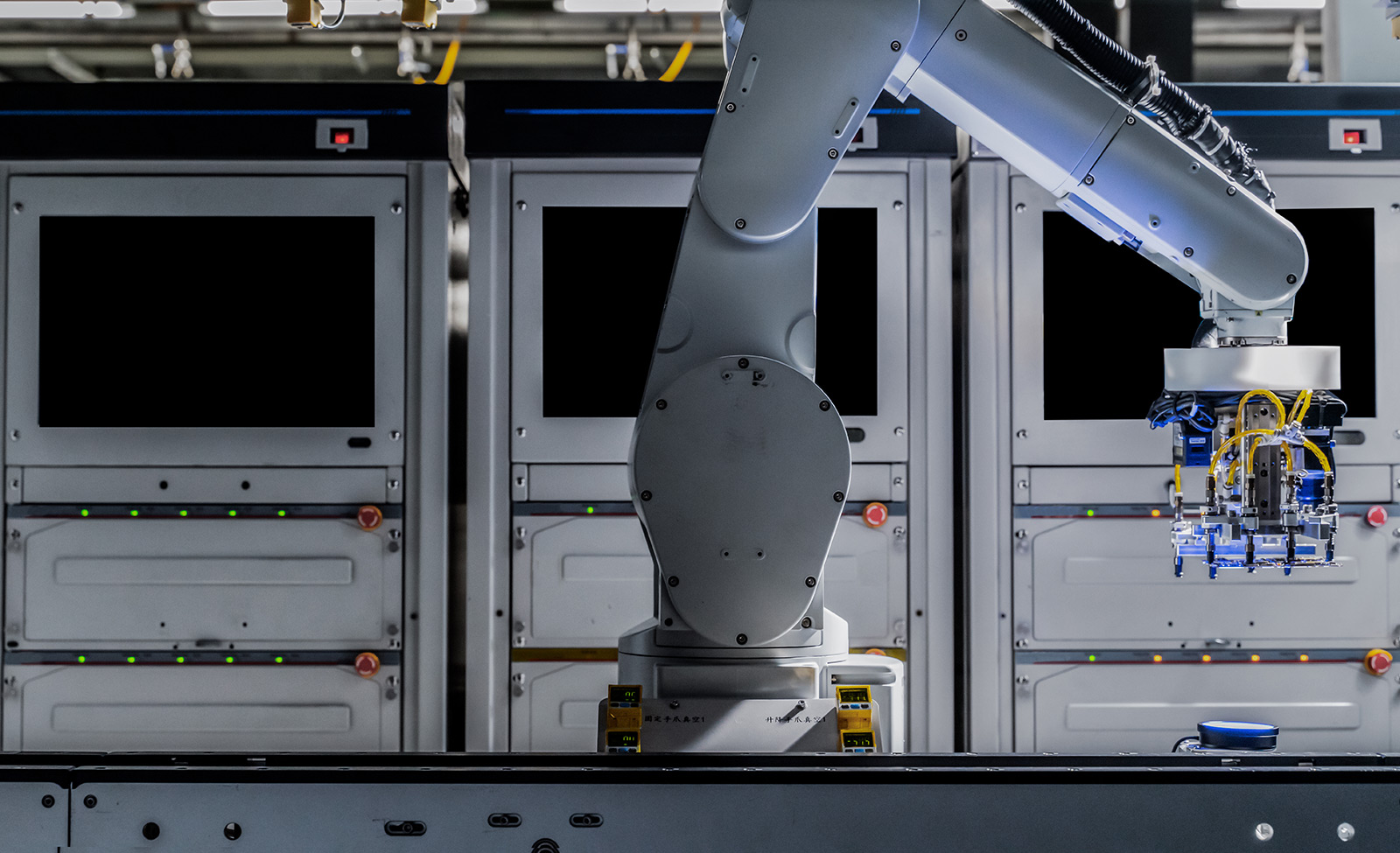
Рабочие нужны для того, чтобы визуально проверять, как выглядят корпуса телефонов и экраны, не появилось ли потертостей или каких-то дефектов. Маловероятно, но такое все же возможно. Они протирают экраны, убирают на боковых поверхностях пленку, следят, чтобы не было царапин. И отправляют устройства дальше.
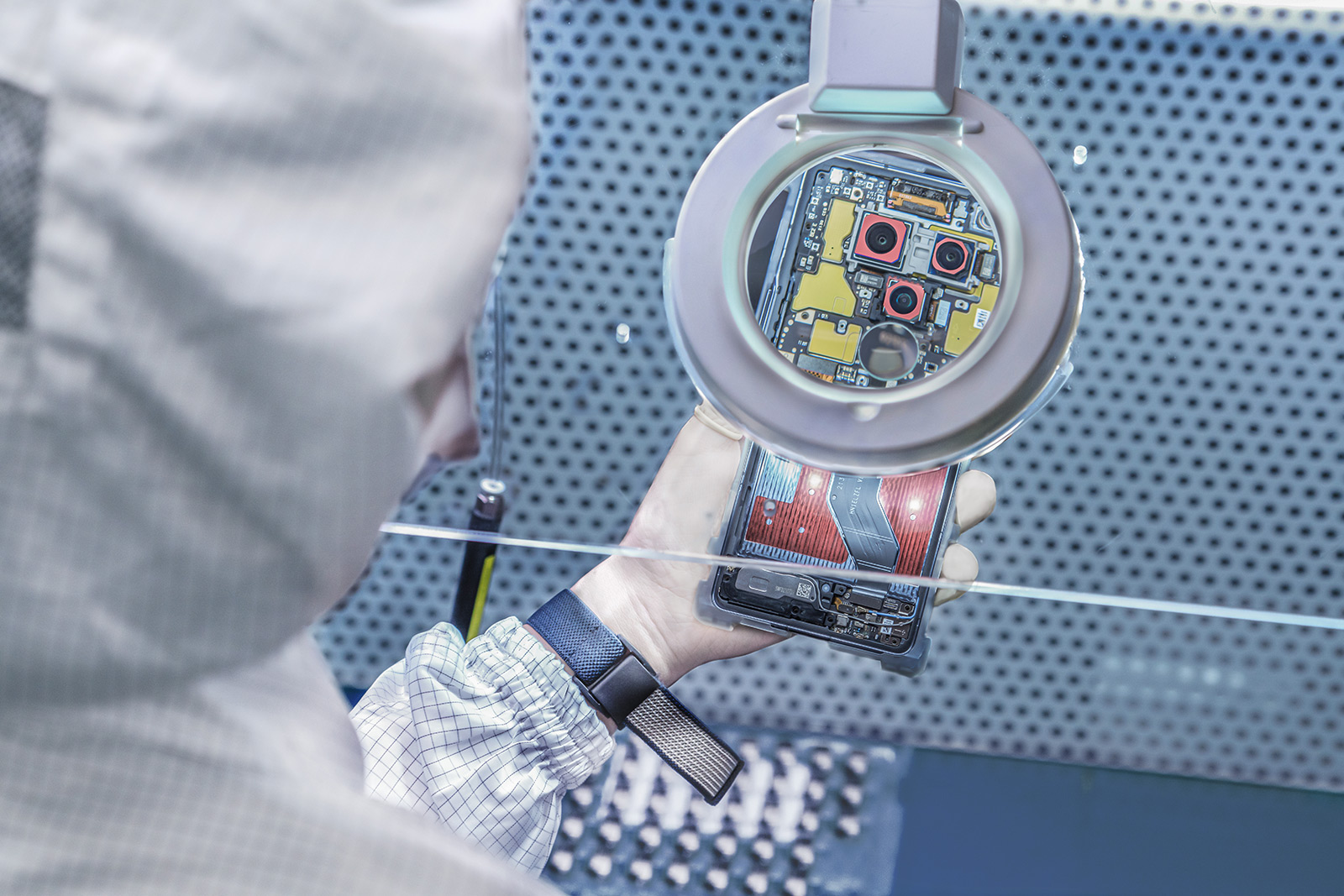
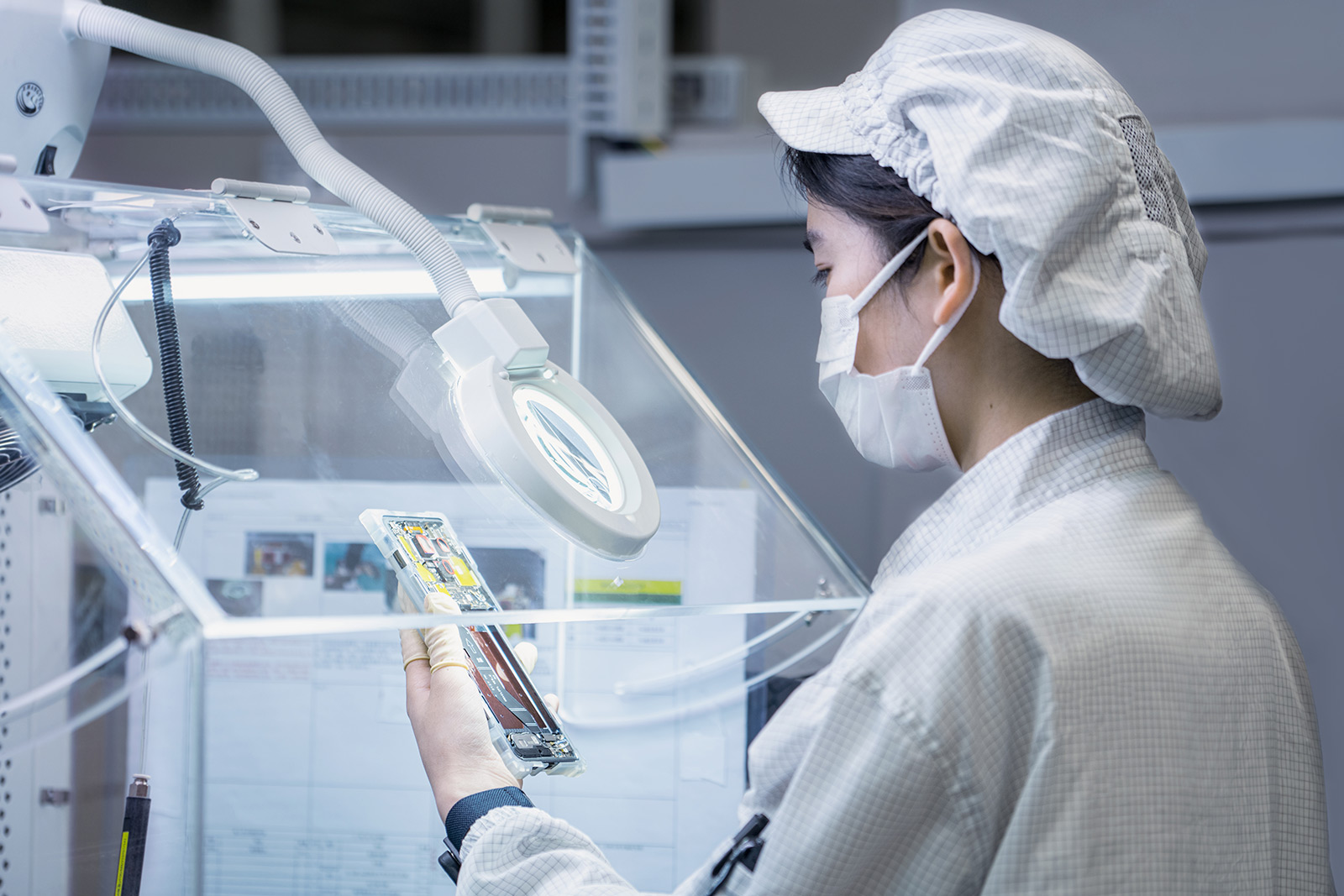
Если кто-то в рознице вам скажет, что царапины на экране или корпусе телефона — это заводской брак, смело игнорируйте такое утверждение, аппарат повредили в той самой рознице. С конвейера они выходят в отличном состоянии.
Как видите, рабочие выполняют функцию дополнительного контроля, причем зачастую они соревнуются с машинами. То есть линия обучается и настраивается так, чтобы люди дублировали те или иные функции, за счет этого и растет автоматизация. Как только появится софт, умеющий определять царапины так же быстро и качественно, автоматизация линии вырастет еще на пару процентов, от людей откажутся и для этой операции. Не думаю, что в конечном итоге линия будет автоматизирована на 100%, в конце концов, нужно подносить компоненты, проверять работу машин, но 90-95% — это вполне достижимая цель.
Помните цифру в 28.5 секунд, что была названа в самом начале? Попытал инженера, и он поделился другими цифрами, выводы никакие делать не буду, но дам их вам для размышлений. В течение суток одна линия производит примерно 4000 смартфонов (обычные модели, не с гибким экраном). То есть смена в 8 часов дает 2000 телефонов. На полный цикл производства телефона уходит до 50 часов. Для смартфонов с гибкими экранами время производства и всех тестов на линии удваивается, это более сложный продукт.
За разговорами мы идем вдоль линии и упираемся в стол, где расставлены разные предметы — жидкое мыло в больших упаковках, рисоварка, чайник, термос и другие бытовые приборы. Все новенькое, очень дешевое даже для Китая. Напротив каждой кучки товаров расположены значки со звездами. Это система мотивации рабочих, раз в неделю они могут выиграть эти призы, если не допускают никаких ошибок в своей работе. Товары копеечные, заинтересованность людей в таком соревновании показывает их уровень жизни. Попытка расспросить инженера о системе мотивации наталкивается на стандартный ответ: «Наши рабочие живут очень хорошо, они получают в среднем на 40% больше, чем на других заводах». И я даже верю, что это так. Но разглядывая копеечное мыло, за которое борются рабочие, я понимаю, что уровень их жизни довольно низок.
Стоимость автоматизированных линий постоянно растет, также как и их сложность. А вот цена рабочих рук меняется не так сильно, но только автоматизация позволяет добиться таких результатов, как на фабрике Honor. Задал вопрос, сколько устройств отбраковывается на линии в процессе производства, они в зависимости от типа брака возвращаются на переработку. Ответ пришлось узнавать, так как в памяти этого не было, оказалось, что это число значительно меньше, чем даже один процент, примерно один телефон на десять тысяч. И то в большинстве случаев это небольшая царапина где-то на корпусе, что позволяет его быстро переработать, сбой в электронике почти невообразим.
Помимо производства, мы заглянули в дата-центр, исследовательские лаборатории, а я даже побродил без присмотра по коридорам и наткнулся на любопытные вещи. Но об этом — в отдельном материале, тут же мы говорили о производственных линиях и об их автоматизации. Надеюсь, что этот материал расширит ваш кругозор и покажет, насколько производители контролируют каждый этап производства, насколько точно знают о том, что на нем происходило, и могут поднять все данные об этом. Миллионы смартфонов Honor производятся на этом заводе, а объем производства можно с легкостью удвоить. Так что потенциал тут далеко не раскрыт, и в будущем эта фабрика может проявить себя еще лучше.
Тревожно как-то. Финансовая элита сменяется высшим хай-теком.
Раньше Европа радела за автоматизацию, так как только с ее помощью могла соревноваться по цене товаров с Китаем. А сейчас, когда и Китай переходит на автоматизацию, шансов у "богатых" стран становится все меньше…
Honor молодцы. Очень хотелось бы современную модель, как раньше Honor 9x, без выреза под камеру на экране.
Был там же по приглашению, в R&D, на производстве и в ШК, но в ZTE, все ровно также выглядит, один в один и даже территориально в Шэньчжэне они расположены в одном кластере.Шэньчжэнь, как город, сам по себе крут до невозможности.
Можно конечно верить в то что добрая Ху подарила Хо новый завод… Но даже мои тапки смеются с такого расклада…
Mikhail Volkov, За себя тревожиться надо, а не за участников этого жабогадюкинга 🙂
А мне казалось что хуавей и хонор делают на одном заводе. Почему у них все одинаково
Что-то на счёт раз не заметил в ящике с телефонами айфонов — большинство точно на андроид.А про мотивацию рисоварками — ну что же, полезная в хозяйстве вещь, не майбах же выдавать ;-)В СССР вообще вымпелы на время выдавали — и люди старались ;-)Да и зарплата рабочих получается прям сильно больше средней российской.Архитектура интересная зданий и заводов..Понятно, что близость Ху и Хо — это секрет Полишинеля.Но тут смотрю, чипсеты Qualcomm стали у Honor появляться.Наверное примерное так же по тихому и наши санкции будут уменьшаться, денежек то хочется 😉
>нужно было сдать все устройства, их складывали в отдельный ящик.Несколько Huawei и Honor, Samsung, Xiaomi. А владелец единственного iPhone пользуется еще и Honor V2.
Вот это хороший материал, с интересом почитал! Спасибо!
Автор мимоходом намекает, что до триумфального возвращения Huawei осталось полтора-два года. Но и Honor тоже молодцы.
Традиционное спасибо за "путевые заметки". Эльдар, пишите книгу!
Скажите, для чего нужно 2 смартфона? Особенно, когда это 2 ультра большие и мощные лопаты? В то время, когда каждый телефон сейчас работает без проблем с 2мя симками? Смотрю вот на фото, почти у всех 2 смартфона. Интереса ради, сценарии использования и почему нельзя обойтись одним.
Артур Буттаев, Подключить к системам компании, например, чтобы иметь возможность видеть корп почту и впн с телефона — телефон администрируется удалённо компанией. На него как-то страшно ставить что-то личное
спасибо за экскурсию, Эльдар!
Так что там с зарплатами?